Command & Control Lead
M-1 Command & Control - investigation situation
M-1.1 Contents
⚙ M-1.1.1 Global content
Command & Control: describing the processes being processed.
The information explosion. The change is the amount we are collecting measuring processes as new information (edge).
📚 Information questions Why.
⚙ how to do measurements for information.
🎭 What to do with new information insight?
⚖ legally & ethical acceptable?
When wanting going logical backward:
🔰 Too fast ..
previous.
⚙ M-1.1.2 Local content
Reference | Squad | Abbrevation |
M-1 Command & Control - investigation situation | |
M-1.1 Contents | contents | Contents |
M-1.1.1 Global content | |
M-1.1.2 Local content | |
M-1.1.3 Guide reading this page | |
M-1.1.4 Progress | |
M-1.2 Floor plans, ordered dimensions | C6isrist_02 | I_Floor |
M-1.2.1 Multidimensional contexts | |
M-1.2.2 The Siar model | |
M-1.2.3 Multidimensional ordered contexts | |
M-1.2.4 Advanced PDCA DMAIC understanding: Lean | |
M-1.3 Steering roles tasks | C6isrist_03 | C_Tasks |
M-1.3.1 With what to start understand steering? | |
M-1.3.2 How tot steer, understanding improvements | |
M-1.3.3 Strategy Who: Hoshin Kanri, Vision, Mission | |
M-1.3.4 Strategy Levels in the organisations | |
M-1.4 Culture building people | C6isrist_04 | H_Culture |
M-1.4.1 Understanding, awareness of the situation | |
M-1.4.2 Having respect for people | |
M-1.4.3 Understanding the strategy the goal | |
M-1.4.4 Strategy execution with insight | |
M-1.5 Sound underpinned theory, foundation | C6isrist_05 | C_Theory |
M-1.5.1 Information processes basic lean requirements | |
M-1.5.2 Ideas from an anatomy, routes by maps, usefulness | |
M-1.5.3 Process foundation, the fundaments basic creation | |
M-1.5.4 Information processes controlled evaluated changes | |
M-1.6 Maturity 0: Strategy impact understood | C6isrist_06 | CMM0-SIM |
M-1.6.1 Determining the position, the situation | |
M-1.6.2 Determining the destination, strategy | |
M-1.6.3 Managing Uncertainties, confusion, ambiguities (MUCA) | |
M-1.6.4 Ambiguity in dimensions: foundation floorplan | |
M-2 Command & Control gaps understanding and solutions | |
M-2.1 Seeing ICT Service Gap types | C6isrhow_01 | 👁-GAP |
M-2.2.1 Understanding safety, functionality by requirements | |
M-2.2.2 Changing safety or functionality | |
M-2.2.3 Safety technology alignment | |
M-2.2.4 Safety information, data, alignment | |
M-2.2 Floor plans, seeing value streams | C6isrhow_02 | T_Value |
M-2.2.1 Standard patterns information flows, process changes | |
M-2.2.2 Information, process flow - change flow | |
M-2.2.3 Processing information vs industrial differences | |
M-2.2.4 Using the portfolio management system Jabes | |
M-2.3 How to steer in the information landscape | C6isrhow_03 | C_Steer |
M-2.3.1 Strategy learning, improvements | |
M-2.3.2 The practical Value stream map, VaSM | |
M-2.3.3 Defining, analysing the value stream | |
M-2.3.4 Getting value from the value stream | |
M-2.4 Roles tasks in the boardroom | C6isrhow_04 | C_Culture |
M-2.4.1 Changing role C-level | |
M-2.4.2 Steering changing roles (I) | |
M-2.4.3 Steering changing roles (II) | |
M-2.4.4 Transforming steering roles | |
M-2.5 Sound underpinned theory, operations | C6isrhow_05 | ✅-logic |
M-2.5.1 Simf: the complete operational flow cycle | |
M-2.5.2 Simf: the complete desing & build flow cycle | |
M-2.5.3 Realisation, control & command dimensions seen outside | |
M-2.5.4 Antipodes in Simf and maturity levels | |
M-2.6 Maturity 3: Enable strategy to operations | C6isrhow_06 | CMM3-SIM |
M-2.6.1 Short term results or long term results (I)? | |
M-2.6.2 Short term results or long term results (II)? | |
M-2.6.3 A portfolio with specfication | |
M-2.6.4 Purposeful products, services by an organisation | |
M-3 Command & Control innovations and the future | |
M-3.1 Information processing in the information age | C6isrsll_01 | I_Sage |
M-3.1.1 Effectivity, efficiency, lean, agility | |
M-3.1.2 Safety, Cyber security | |
M-3.1.3 Knowing, managing, information customer related | |
M-3.1.4 Knowing, managing, process results customer related | |
M-3.2 Floor plans, optimizing value streams | C6isrsll_02 | I_Serve |
M-3.2.1 Aligning the Service organisation to the information age | |
M-3.2.2 Abstraction levels, closed loops in information context | |
M-3.2.3 Understanding information, from data to insight | |
M-3.2.4 Aligning service provision in the information age | |
M-3.3 Why to steer in the information landscape | C6isrsll_03 | C_Edge |
M-3.3.1 Customer centricity value streams | |
M-3.3.2 Failing management signals | |
M-3.3.3 learning - lean accounting | |
M-3.3.4 Multiple dimensions, Antipodes asteroide world | |
M-3.4 Visions & missions in the boardroom | C6isrsll_04 | C_Vision |
M-3.4.1 Structuring, engineering the enterprise | |
M-3.4.2 Enterpise structuring: cycles & multiple dimensions | |
M-3.4.3 Optimising flows: removing constraints | |
M-3.4.4 Optimising flows: budget, design, production | |
M-3.5 Sound underpinned theory, improvements | C6isrsll_05 | ✅-dimensions |
M-3.5.1 A structured enterprise, organisation | |
M-3.5.2 Change process in a structured enterprise, organisation | |
M-3.5.3 Changing the structured enterprise, organisation | |
M-3.5.4 Three dimensional anatomy maps, PDCA cycles | |
M-3.6 Maturity 5: Strategy visions adding value | C6isrsll_06 | CMM5-SIM |
M-3.6.1 The product, service positioned within a system | |
M-3.6.2 Compliancy at an organisation, products, services | |
M-3.6.3 Optimizing an organisation, products, services | |
M-3.6.4 The purposeful organisation, products, services | |
M-3.6.5 Following steps | |
⚖ M-1.1.3 Guide reading this page
Command & Control Abstraction and models
This page is about
Command & Control
C6ISR command, control, communications, computers, cyber-defense and combat systems and intelligence, surveillance, and reconnaissance.
Just replace "combat systems" into "commercial systems" and we can proceed for a generic applicable abstraction for all systems.
I am not experienced in this command & control area although experienced by their effects.
My observations and collecting from a lot of others in trying to connect what control & command is and how it is entangled into information processing.
There are an incredible number of good usable models out there, but we've lost our way by getting too caught up in the tech buzz.
What we're doing is exchanging pretty abstract ideas between people with language and pictures.
Command & Control: Technology vs Organisation
❶ Guidance is: "Command... Control... in the Information Age"
Power to the Edge (David S. Alberts, Richard E. Hayes 2003)
Focusing upon improving both the state of the art and the state of the practice of command and control, the CCRP helps DoD take full advantage of the opportunities afforded by emerging technologies.
The source is defence but mentioned is that is generic appplicable.
This book explores a leap now in progress, one that will transform not only the U.S. military but all human interactions and collaborative endeavors.
Power to the edge is a result of technological advances that will, in the coming decade, eliminate the constraint of bandwidth, free us from the need to know a lot in order to share a lot, unfetter us from the requirement to be synchronous in time and space, and remove the last remaining technical barriers to information sharing and collaboration.
Our behaviors and the architectures and characteristics of our systems are driven by economics, in this case the economics of information.
The dawn of the Information Age was ushered in by Moore's Law.
As the cost of computing fell, we stopped focusing our attentions on conserving available computing resources and began to be inefficient consumers of computing resources.
❷ The document is not well known but reading it, it promotes lean agility in a way not being locked in anymore by a cultural example.
What to do about this?
- The source that referred me to this document got very upset when I interpreted it as vision for promoting lean agility in a changing world.
The only explanation for that is being hurt by bad experiences in wrong management approaches.
It is alarming signal that a lot of damage has been done to achieve a change into new information age.
- Just reading some vocabulary, avoiding confusion:
- Terms of references , TOR show how the object in question will be defined, developed, and verified.
They should also provide a documented basis for making future decisions and for confirming or developing a common understanding of the scope among stakeholders.
In order to meet these criteria, success factors/risks and constraints are fundamental. They define the:
- vision, objectives, scope and deliverables (i.e. what has to be achieved)
- stakeholders, roles and responsibilities (i.e. who will take part in it)
- resource, financial and quality plans (i.e. how it will be achieved)
- work breakdown structure and schedule (i.e. when it will be achieved)
- stakeholders
Project stakeholder refers to "an individual, group, or organization, who may affect, be affected by, or perceive itself to be affected by a decision, activity, or outcome of a project, program, or portfolio."
ISO 21500 uses a similar definition.
- Stovepiping is the presentation of information without proper context. ...
Another meaning of stovepiping is "piping" of raw intelligence data directly to decision makers, bypassing established procedures for review by professional intelligence analysts for validity (a process known as vetting), an important concern since the information may have been presented by a dishonest source with ulterior motives, or may be invalid for a myriad of other reasons.
Intelligence organizations may deliberately adopt a stovepipe pattern so that a breach or compromise in one area cannot easily spread to others.
- A stovepipe organization (alt organisations) has a structure which largely or entirely restricts the flow of information within the organization to up-down through lines of control, inhibiting or preventing cross-organisational communication.
Many traditional, large (especially governmental or transnational) organizations have (or risk having) a stovepipe pattern. In the IT-jargon: siloed organisations.
😉 There is a connection for vision, strategy.
Optimizing governance in the organisation for the service
❸ Where tot optimize is another question than what to optimize, the difference is important. (Kevin Kohls 2024)
Understanding the Theory of Constraints: Much More Than Production
The goal of TOC is always system optimization, not local optimization.
System metrics, such as overall throughput, cycle time, and variability, must be optimized for the entire production system.
In contrast, trying to improve efficiency at each individual station is called local optimization, which often leads to suboptimal results for the broader system.
😉 There is a connection for optimizing systems, lean.
Optimizing governance and accountability
❹ It was assumed only a technical only state of the art report. Then seeing: (pag 63, 66)
Microsoft Digital Defense Report 2024 "our customer base and the role" expectations from customers.
Organizations should focus their security culture and governance efforts on accountability, teamwork, and shared responsibility.
Accountability always starts at the top, with organizational leaders who not only understand their responsibility for security outcomes but ensure that security risk management is embedded across their business in an organization-wide and collaborative way.
Leaders must establish a system of accountability, prioritization, and aligned incentives that is executed and monitored across the organization.
They must delegate risk accountability, mitigation implementation responsibility, and associated budgets/costs to leaders, managers, and individual contributors, as accountability alone cannot create a healthy culture.
we have found that an organization's resilience maturity can be determined based on four pillars: Operational, Tactical, Readiness, and Strategic. Maturity in each of these pillars is categorized as either Basic, Moderate, or Advanced.
😉 There is a connection for systems entangled with safety.
⚒ M-1.1.4 Progress
done and currently working on:
- 2020 week 44
- Was set up for the sentence: data is the new oil.
- 2024 week 40
- Web content redesign with Jabes being pivotal started for this page.
- Adding the C6isr replacing data for stovepipes opened the next steps.
- The goal for command & control has become more clear by:
- Knowing what the conceptual gaps in command & controls are
- Insight needed improvements according Gemba, shop-floor
- The old content moving to the technical system serve area.
- 2024 week 43
- With the trigger of SIMF the first six chapters is getting a holding with strategy in the information age.
Much about strategy is collected from advisory sources.
- 2024 week 45
- Getting around to the whole in the analysis the last six chapter are becoming in a direction of inter relationships and goals.
- 2024 week 46
- Getting around to the whole in the analysis the middelt six chapter are getting completed in line of the others.
- 2024 week 47
The cycle at technology, plane 2/3 was wrong figured.
There is a V-shape at engineering, building, validating.
The same approach is at the other parts in the cycle.
Only the portfolio suggestions, backlog and the portfolio product specifications are stable in some moment in time.
Changed V-shapes, triple-V, for:
- Suggestion box, backlog into requirements: Wedge model, double-u.
- Validations of the service, product into specifications: triple-u.
Planning to do & changes:
- The structure at technology, plane 3/4 is incomplete.
There should not direct external topics but onely roles, activities (2024 wk47).
Technology:
- Security operations centre (SOC) with several focus area's.
- Identity & Access (IAM) - data quality (DQ).
- Incident repsonse (IRT) - Continuity availablity (DR).
Functionality:
- Information quality (IQ) with several focus area's.
- Information registration, history (HIS) - Information context, master data (DA-MD)
- Vendor management, procurement - Technical compliancy alignment (TAC).
M-1.2 Floor plans, ordered dimensions
Building any non trivial construction is going by several stages.
These are:
- high level design & planning
- detailed design & realisation
- evaluation & corrections
Non trivial means it will be repeated for improved positions.
Before any design, tools are needed for measuring what is going on.
Without knowing the situation or direction there is no hope in achieving a destination by improvements.
⚖ M-1.2.1 Multidimensional contexts
Control & command lost in space
(Power to the edge)
The Industrial Age applied a “divide and conquer” mentality to all problems.
Academic disciplines, businesses, associations, and military organizations defined their roles as precisely as possible and divided their overall activities into coherent subsets that could be mastered with the existing knowledge, technologies, and personnel. ...
If a sound set of decompositions is made, then these organizational subsets of the organization (again, a business, bureaucracy, or military organization) can develop professional specialties that help the overall organization or enterprise to perform its mission and achieve its objectives. ...
The Industrial Age raised specialization to heights not previously contemplated.
The whole idea of an assembly line in which a set of carefully sequenced actions generates enormous efficiency was unthinkable before this era. ...
The organizational consequence of Industrial Age specialization is hierarchy.
The efforts of individuals and highly specialized entities must be focused and controlled so that they act in concert to achieve the goals of the larger organizations or enterprises that they support.
This implies the existence of a middle management layer of leaders whose tasks include:
- Understanding the overall goals and policies of the enterprise;
- Transmitting those goals to subordinates
- Developing plans to ensure coordinated actions consistent with the organization's goals and values;
- Monitoring the performance of the subordinates, providing corrective guidance when necessary; and
- Providing feedback about performance and changes in the operating environment to the leadership, and making recommendations about changes in goals, policies, and plans.
The size and the number of levels that separate the leader(s) of an enterprise and the specialists that are needed to accomplish the tasks at hand are a function of the overall size of the enterprise and the effective span of control, that is, how many individuals and/or organizational entities that can be managed by an individual or entity
(page 41)
❶ With that approach situational awareness in the working force was not required.
Perhaps the most famous quotation about planning from that era (all the more relevant because it was uttered by one of the great planners in history) is, “No plan survives first contact with the enemy.”
(page 47)
❷ Able to act on change what is expected is required in the information age.
Industrial Age organizations are not optimized for interoperability or agility.
Thus, solutions based upon Industrial Age assumptions and practices will break down and fail in the Information Age.
This will happen no matter how well intentioned, hardworking, or dedicated the leadership and the force are.
(page 56)
❸ Able to act on change what is expected is required in the information age.
The result is that, as some have put it, “everyone needs to talk to everyone.” We would put it a slightly different way.
Since one cannot know who will need to work with our systems and processes, they should not be designed to make it difficult to do so.
On the contrary, they must be built to support a rich array of connectivity to be agile.
The same is true with our processes. They need to be adaptable in terms of who participates as well as who plays what roles.
(page 59)
😉 The change to unlearn and learn: everybody needs to understand the shared goal and able to understandable communicate to their counterparts.
The Shop floor, mapping activities flows to maps
Cartography,
the art and science of graphically representing a geographical area, usually on a flat surface such as a map or chart.
It may involve the superimposition of political, cultural, or other nongeographical divisions onto the representation of a geographical area. ...
The procedures for translating photographic data into maps are governed by the principles of photogrammetry and yield a degree of accuracy previously unattainable.
The remarkable improvements in satellite photography since the late 20th century and the general availability on the Internet of satellite images have made possible the creation of Google Earth and other databases that are widely available online.
😉 Similarity to unlearn and learn: becoming aware in the location, situation.
Anatomy, Data literacy
Anatomy,
involves the study of major body structures by dissection and observation and in its narrowest sense.
By the end of the 19th century the confusion caused by the enormous number of names had become intolerable.
Medical dictionaries sometimes listed as many as 20 synonyms for one name, and more than 50,000 names were in use throughout Europe. ...
In 1887 the German Anatomical Society undertook the task of standardizing the nomenclature, and, with the help of other national anatomical societies, a complete list of anatomical terms and names was approved in 1895 that reduced the 50,000 names to 5,528. ...
The Terminologia Anatomica, produced by the International Federation of Associations of Anatomists and the Federative Committee on Anatomical Terminology (later known as the Federative International Programme on Anatomical Terminologies), was made available online in 2011.
😉 Similarity to unlearn and learn: an agreement in shared vocabulary in communications.
⚖ M-1.2.2 The Siar model
The process life cycle, static & dynamic
❹ Mindset prerequisites 👉🏾 Siar model
The static element information is well to place. A rectangular, box, is a fit for the static representation.
😉 The model, static, covers all of:
- value stream: left to right
- PDCA, DMAIC, lean agile improvements
- simple processes: 0 - 9
- The duality between processes, transformations, and information, data
- four quadrants:
- I Push, IV Pull
- III lean agile requests. II deliveries
😉
Processing, transforming, is a dynamic process.
A circular representation is a better fit.
The cycle:
- Ideate - Asses
- Plan - Enable
- Demand, Backend
- Frontend , Delivery
Customer interaction: bottom right side.
Supply chain interaction: bottom left side.
- realistic human interaction & communication. nine plane:
- Steer Shape Serve
- Strategy, Tactics, Operational
- Accountabilities, responsibilities, roles
Situation awareness
❺ Situational awareness
or situation awareness (SA) is the understanding of an environment, its elements, and how it changes with respect to time or other factors.
Situational awareness is important for effective decision making in many environments. It is formally defined as:
🎭 the perception of the elements in the environment within a volume of time and space, the comprehension of their meaning, and the projection of their status in the near future.
The formal definition of SA is often described as three ascending levels:
- Perception of the elements in the environment,
- Comprehension or understanding of the situation, and
- Projection of future status.
People with the highest levels of SA have not only perceived the relevant information for their goals and decisions, but are also able to integrate that information to understand its meaning or significance, and are able to project likely or possible future scenarios.
These higher levels of SA are critical for proactive decision making in demanding environments.
The mindset by the SIAR model is used over and over again.
PDCA, DMAIC, OODA
❻ Focus on Outcomes or Face Failure:
- DMAIC is an abbreviation of the five improvement steps it comprises: Define, measure, analyze, improve and control.
All of the DMAIC process steps are required and always proceed in the given order.
- ADKAR is similar:
- Awareness (of the need for change)
- Desire (to participate and support the change)
- Knowledge (on how to change)
- Ability (to implement required skills and behaviours)
- Reinforcement (to sustain the change)
-
PDCA or plan do-check-act is an iterative design and management method used in business for the control and continual improvement of processes and products.
- The OODA loop (observe, orient, decide, act) is a decision-making model developed by United States Air Force Colonel John Boyd.
He applied the concept to the combat operations process, often at the operational level during military campaigns.
It is no silverbullet.
-
The OODA loop is merely one way among a myriad of ways of describing intuitive processes of learning and decision making that most people experience daily.
It is not incorrect, but neither is it unique or especially profound.
in a figure:
see right side.
⚖ M-1.2.3 Multidimensional ordered contexts
Ordered for customer processes
❼ The goal is drawing a floorplan (virtual).
Ordered dimensions for supporting the external customer.
This is the complete value stream.
😉 Goal: who, customer demand delivery.
Architecting, designing, building has some of the dimensions in the axis mirrored.
Ordered for internal processes
❽ The goal is drawing a floorplan (virtual).
Ordered dimensions for supporting the service.
Depending on the strategy it is innovation of a product of part of value stream for a complicated project product.
😉 Goal: which, product quality quantity.
Architecting, designing, building has some of the dimensions in the axis mirrored.
⚖ M-1.2.4 Advanced PDCA DMAIC understanding: Lean
Why: PDCA - DMAIC - SIAR , lean
❾ This is the third SIAR image: dynamic, static & stages for flow & control.
Change:
PDCA
DMAIC
- define, measure,
- analyze, improve
- control
SIAR
- situation,
- input/initiative
- activity/analyse
- result/request
OODA
- Observe
- Orient
- Decide
- Act
Information, data, processing adding measurements for understanding value creation:
- functionality: Processes, Practices, Instructions, Services
- functioning: Measurable, Efficient, Effective, Valuable
- Applied closed loops by: Data, Information, Knowledge, Insight
Going for lean, Genba-1
❿ Lean in a 3*3 plane is innovative idea. It is a result of combining the SIAR model to lean.
The lean philosophy in a 9-plane figure,
see right side.
Not only:
🎭 pillars, bars,
🎭 or diagonals,
🎭 edges - moderators
🎭 but also repetitive clockwise cycles.
Each pillar is bottom up from a novice to a master mind.
- ❶ ❷ ❸ The left pillar is what organisational leaders are supposed to do.
- ❹ ❻ The middle pillar is what a technical leader can do.
- ❼ ❽ ❾ The right pillar is where an advisor can help.
- ❺ In the middle the strategic goal and the threats.
It are the organisational leaders enabling this, but where to start?
- Have the strategic goals translated in something measurable, goal: closed loops.
- Go around clockwise from the right bottom corner.
- Continous repeat the cycle holding of threats improving the set goals.
A viable system, biotope
A very different aspect for information processing is: seeing it by components in a viable system.
"The formal viable system theory is normally referred to as viability theory, and provides a mathematical approach to explore the dynamics of complex systems set within the context of control theory.""
gives the reference to:
closed loop control, the control action from the controller is dependent on the process output.
The
Chemistry
is the scientific study of the properties and behavior of matter.
It is a physical science within the natural sciences that studies the chemical elements that make up matter and compounds made of atoms, molecules and ions: their composition, structure, properties, behavior and the changes they undergo during reactions with other substances.
This comes back to:
Petri Net
is one of several mathematical modeling languages for the description of distributed systems.
It is a class of discrete event dynamic system. A Petri net is a directed bipartite graph that has two types of elements: places and transitions.
Like industry standards such as UML activity diagrams, Business Process Model and Notation, and event-driven process chains, Petri nets offer a graphical notation for stepwise processes that include choice, iteration, and concurrent execution.
Unlike these standards, Petri nets have an exact mathematical definition of their execution semantics, with a well-developed mathematical theory for process analysis.
There are three type of systems within a viable one :
- Autonomic nervous system
The autonomic nervous system is a control system that acts largely unconsciously and regulates baisc functions
- Consciousness decisions.
Philosophers have used the term consciousness for four main topics: knowledge in general, intentionality, introspection (and the knowledge it specifically generates) and phenomenal experience.
- Complex adaptive systems.
A CAS is a complex, self-similar collectivity of interacting, adaptive agents. Complex Adaptive Systems are characterized by a high degree of adaptive capacity, giving them resilience in the face of perturbation.
M-1.3 Steering roles tasks
Managing the building any non trivial construction follows several stages.
These are:
- high level design & planning
- detailed design & realisation
- evaluation & corrections
Non trivial means it will be repeated for improved positions.
Managing the process, information is needed for understanding what is going on.
Without knowing the situation or direction there is no hope in achieving a destination by improvements.
⚖ M-1.3.1 With what to start understand steering?
Strategy
😉 Dr. Marc Sniukas made a presentation on this topic that got much attention.
It is 20 years ago (2004) but still a great resource.
Last updated in 2011, the theory is generic.
Porter's Five Forces.
It is the answer to:
What drives competition in the industry?
The question in this what is the orientation, the flow and change expectations?
A variation and extension to the basic version.
In a figure,
see right side.
⟲ Turn it 90° counter clockwise.
- New entrants to Act on. Situation for substitutes & complementors.
- The flow will be: Input = suppliers left to right into buyers = Result.
- The change starts:
- (pull) by political/regulatory drivers, to socio-cultural drivers.
- (push) in economic drivers to technology drivers.
Value stream
From the presentatiation (Sniukas): 👉🏾
An activity system is an integrated set of value creation processes leading to the supply of product and/ or service offerings.
This activity system is frequently referred to as the value chain. (Porter, 1985)
⚖ M-1.3.2 How tot steer, understanding improvements
C-level Vision misundertanding
A reactions in the LI-post (Manuel Bogado Gudsvän):
What is strategy? (2024 M. Sniukas)
Maybe to reduce the concept of Strategy to "business strategy" is the core reason on why "nobody really knows what strategy is".
Using the analogy of the elephant and different blinded people giving different opinions according to their "point of touch":
it could be compared to someone asking "what is an animal?" and the observer answers: "An elephant".
Because he might see all of the elephant, but despite that, an elephant per se is not the real definition of an animal, but an example.
Therefore, In the case of "Strategy" the true source must not be "business", but the "inventors" of the word "Strategy".
➡ What was the ancient greek art of the strategos?
In this case and according to historians and philosophers (not business people) Alexander the Great and other greek strategist are closer to Strategy than any business guru.
Because it is the original and fundamental source.
Once we know the mind of AIexander, Philip II, Julius Cesar, Hannibal, only then we could obtain the secret of Strategy (that said by Napoleon himself).
If we know the fundamentals, then we know all the colors.
Afterwards colors can be applied anywhere (i.g. business) and in different combinations according to the power of execution of the strategist.
Steer in continuous improvement
Kaizen is much more than process improvement. It's a self improvement process!
Respect for People starts with each one of us, individually! (repost of David Bovis, M. npn)
Got the reply (Kevin Kohls oct 2024) :
😉
An ideal vs. reality. It's great to hope this occurs, but to rely on it means we are "addicted to hopium."
Any change to a current established methodology, valid or not, will cause conflict. ...
A key aspect of Holistic Thinking is understanding "how to cause the change.":
- What is the motivation behind the business culture we live in?
- What is the goal, or a requirement for the goal, of every one of these businesses?
- What is the one metric for which CEOs, the ultimate customers/supporters of our CI process, are held accountable?
- What would every employee, especially those in a union, like to see improve due to a successful Kaizen event that also positively impacts their personal lives?
- What would an employee like to see as a cause-and-effect outcome of their efforts?
Hitozukuri (sometimes spelled Hitozokuri) is a Japanese concept that translates to "building people" or "developing people."
⚖ M-1.3.3 Strategy Who: Hoshin Kanri, Vision, Mission
C-level Vision retroperspective
What the heck is strategy anyway? (2024 M. Sniukas)
For more than 20 years, I've been exploring the answer to that question.
About 20 years ago, I made a presentation on this topic that got much attention.
This presentation, viewed by hundreds of thousands and ranked in the top 1% on Slideshare, was a significant milestone in my journey.
It was a big deal at the time, and its popularity speaks to the relevance of the topic.
I've updated the presentation a few times since then.
Here's a version from 2011 that still serves as a great introduction.
If I were to do it again today, I would definitely make some changes to the layout and design. ;-)
Overall, it's still a good way to understand the basics of strategy.
The reference: Strategy: Process, Content, Context? 3rd edition De Wit & Meyer Thomson Learning 2004
"Nobody really knows what strategy is."
Strategy Formation Activities:
😉 Where to start and how to proceed for these 9 pointers in the figure by their positions is unintended a good fit for the SIAR model that extended into Lean understanding.
C-level Vision or plan retroperspective
from a collection of what is about:
most ceos think they have a strategy (2024)
😱
Most CEOs think they have a strategy, they only have a plan. Here’s the difference:
- Strategy is the set of choices that positions you to win.
- Planning is just organizing who does what by when.
Too many companies treat planning as a stand-in for strategy.
The result is
- Without a strategy we fill our time with:
- ... what we want, or
- ... what we think the boss wants or,
- ... by reacting
- Without a strategy, time and resources are waste on piecemeal disparate activities.
C-level Vision, choices in managing creating strategies
😉
tired of your strategy falling flat (2024)
In today's fast-paced business environment, having a clear and effective strategy is more crucial than ever.
Here are six strategy frameworks that can help you structure your thinking, explore innovative paths, and ultimately craft breakthrough strategies:
- who what how: (Costas Markides)
- Who should we target as our customers?
- What products and services should we offer?
- HOW can we best deliver this offering to these customers?
- PLaying To Win Strategy Choice Cascade (PtW): (Roger Martin)
- Winning Aspirations: Our ambitions
- Where to play: Customers, offerings, geographies, channels
- How to win: Low cost or differentiation
- Capabilities: Distinctive capabilities that underpin our HtW?
- Management System: How we build and maintain the capabilities
- Strategy diamond - Similar to the PtW cascade, with a couple of additions.
What I like about the Diamond is its distinction between "differentiators" and "economic logic."
Capabilities and Management Systems are referred to as „supporting organizational configuration“ in this framework, but outside of the Diamond.
(Donald Hambrick and James Frederickson)
- How to win with customers.
- How to win as a business.
- Blue Ocean Strategy ( Chan Kim and Renée Mauborgne)
I think of BOS as less of a strategy framework per se and more of a set of tools that helps you generate answers you can plug into PtW or the Strategy Diamond.
BOS is especially suited for creating new growth businesses, but it can also help you explore ideas for differentiation in your existing businesses.
Strategy is about being different, which requires innovation.
- Strategy Maps ( Robert Kaplan and David Norton )
As strategy needs to be coherent, Strategy Maps help to visualize how the various parts of your strategy fit together and how your choices reinforce each other.
They are good for checking whether your decisions make sense.
Also, think about the various perspectives as follows:
- Financials: Short-term
- Customers: External
- Operations: Internal
- Learning: Long-term
- The Kernel Of Good Strategy (Richard Rumelt)
The core of good strategy is focusing on the crucial challenges that must be solved to achieve your ambitions.
- Provides a diagnosis of that challenge
- Outlines how you're going to deal with the challenge
- A coherent set of actions to implement your solution
In a figure:
⚖ M-1.3.4 Strategy Levels in the organisations
Building a hierarchical strategy
Why Most Strategies Fail
😉 The Fundamental Questions You Need to Answer.
Your strategy discussions need to hit on these four levels:
- Ecosystem strategy
With whom do you compete? With whom do you collaborate?
- Corporate strategy
Which businesses should you be in? Do you diversify to spread risk, or go all-in on integrated synergies?
- Business strategy
How compete in your chosen markets? Identify your customers, define your value proposition, nail your business model, figure out how you'll make money.
- Functional strategy HR, IT, Sales, Marketing, Operations? how do these functions contribute to the overall strategy? Analyze their activities, focus areas, and challenges to ensure they align with the overall strategy.
Forget the fluff.
Answer these questions with precision and clarity.
There is a presentation "what is strategy" (2009 - 2011).
The theory is generic.
In a figure,
see right side.
Building stratevy in a cycle
Strategic Learning
Organizations create their futures through the strategies they pursue.
These strategies may be developed in a thoughtful and systematic way or allowed to emerge haphazardly in a series of random, ad hoc decisions made in response to daily pressures.
But one way or another, the strategy a company follows—that is, the choices it makes—determines its likely success.
Astonishingly: only few executives are able to explain their company's strategy clear and compelling.
A successful strategy is not just a matter of open-ended choice-making.
It is choice-making in service of answering some specific and very important questions.
The answers to these questions will determine your destiny.
The cycle is the same as the PDCA and SIAR cycle, only the orientation is different.
Even the different context for diagonals and horizon vertical is there.
- materialised: Focus (define vision), Align (input) , Implement, Learn (situation)
- change: Insight implications, proposition priorities, Action plan, learning loop
Strategy is a process, not a playbook (A.Nesbiit 2024)
Willie Pietersen pragmatically describes strategy as a process and tool to help us build and lead adaptive organizations.
While the differences are subtle, it's important to remember that significant differences originate in small things.
But what resonated with me was the words he used to connect the elements.
- Insight, not data, drives strategic choice.
- A winning proposition, not just a value proposition, drives action.
- An action plan, not a strategic plan, drives execution
- A learning loop, not just feedback, drives learning.
A generic note:
Consultants love their concepts (the Tooligans) more than the living biotope they work for.
M-1.4 Culture building people
Managing the working force at any non trivial construction is moving to the edges.
The cultural changes are:
- Respect for people, learning investments at staff
- Accepting uncertainties and imperfections
- Trusting the working force while getting also well informed
Non trivial means it will be repeated for improved positions.
Managing the working force at processes, information is needed for understanding what is going on.
Without knowing the situation or direction there is no hope in achieving a destination by improvements.
⚖ M-1.4.1 Understanding, awareness of the situation
Enterprise Ontology
Enterprise Engineering Enterprise Ontology (2006 J Dietz)
The context of "Enterprise Ontology" is far beyond that of just "data - information" it is about most aspects of an enterprise, organisation.
Not just the data - information.
Langefors articulated the concern for the content of information, on top of its form ...
... we need to articulate the concern for the intention of information on top of its content, and develop the ontological view on enterprise.
This separation of intention and content will create a new field "enterprise engineering" and make that intellectually manageable.
The evolutionary levels:
- 1st wave: Data Systems Engineering (datalogical view on enterprise)
- 2nd wave: Information Systems Engineering (infological view on enterprise)
- 3rd wave: Enterprise Engineering (ontological view on enterprise)
😱 The current state of art is: everything is data, not even maturity level 1.
Conclusions in the paper are:
- Enterprise Ontology reveals the essence of an enterprise in a comprehensive, coherent, consistent, and concise way, while reducing complexity by well over 90%.
- Enterprise Architecture guides the (re)design and (re)engineering of an enterprise such that its operation is compliant with its mission and strategy, and with all other laws and regulations.
- The new point of view of EE is that enterprises are purposefully designed and engineered social systems.
The reference to a social system states that most issues in information processing are "organisational" based not, by technical matters.
Separations of concerns.
The figure shows a good way in separation of concerns with the focus on the core business.
There a several layers of processing the B-organisatoin is detailed:
- Action model
- Process model, State model
- splits in UAM ISM C M (?)
However, I-Organisation, D-Organisations, do not have good descriptions.
Ways in separation of concerns.
How the thinking developed to achieve this is not clear, but in a document dated 2006 that gap of information is disclosed.
The separtion of concerns is interesting,not having a clear definition on what those concerns are.
Three siloes:
- coordination, (structure)
- actor and (people)
- production. (processes)
What the ontology areas are from the figure:
| Coordination | Actors | Production |
Strategy | C&C | Managing ICT | floor product owner? |
Tactical | formulating interpreting | Infological | computing reasoning |
Operational | speaking, hearing, writing, reading | Datalogical | Copying, Storing transporting |
⚖ M-1.4.2 Having respect for people
Self organising teams
❸ In line with
Bring Power to the Edge (John J. Sviokla, HBR 2009)
The four fundamental principles of the agile, "edge-based" organization are:
- situational awareness,
- skills,
- values, and
- decision rights.
...
Unfortunately, despite the fact that both our governmental and commercial organizations are also facing a more dynamic and volatile environment, in the main our approach has been to create more monolithic, centralized institutions. ...
What we need is a modular, self-synchronizing system to deal with crises at the edges as they happen. ...
Due to our ruthless quest for efficiency we have squished out many of the buffers that could help blunt the propagation of bad effects on food, assets, and other supplies.
We don't notice if we have gone too far until we really need those buffers. ...
My worry is that in our exurban-super-individualistic-iPod-listening-video-game-playing culture, we have lost the local fabric of self-synchronization, and although the spirit may be there to help each other, the mechanisms to make that spirit effective in practice are lacking. The private sector has not done any better.
We need to reinvent what it means to put power to the edge both for our communities and our companies before the next major disruption hits.
🤔 The priorities are set by the enterprise, organisational missions not by technology.
What is waste, value?
Can you see waste in your organization?
The reality is you cannot.
No one has any idea where an organization is performing non-value adding activities, and wasting capacity.
In small pockets we push for efficiency using mostly wrong metrics or cost as a goal.
In factories, if machines are broken down and people are sitting idle, we might see something is off
(Note: it's a different matter that running machines to full capacity is wrong. And even in factories invisible waste is everywhere).
So is in offices, services, and software development companies.
We have waste everywhere:
- But waste is like water to a fish. Or air to humans.
- It's everywhere. But we feel it only in it's absence.
In services and knowledge work, If we do not focus on removing waste, improving flow and delivering objective value to the customer, being busy becomes the measure of being value adding.
Who are we serving and what are we focusing on?
If people are not serving the customer and not focusing on delivering value to them, we will drive sub-optimal human behavior in our teams and employees.
Being busy:
- Do you know what value is?
- Do you how and where it is delivered?
If everybody is busy all the time, calendars are double/ triple booked, and people are always rushing, most likely you cannot answer the above two questions.
😱 Status: statements about waste but no understanding on the state of value streams.
⚖ M-1.4.3 Understanding the strategy the goal
Value streams, what it is about
USM portal
What is the common denominator?
ChatGPT, when asked to define it, produces this:
A value stream can be defined as the sequence of activities or steps required to deliver a product, service, or solution to customers while adding value and minimizing waste.
It represents the end-to-end flow of processes, information, and resources needed to create and deliver the desired outcome.
All quotes in the previous sections acknowledge indeed that a value stream interfaces with the customer.
It starts and ends with the customer.
But then what is the difference with all the other things we have studied for over 100 years in the customer-provider relationship?
Were those not interactions that started with a customer request?
And didn't we describe those in terms of the realization, up to and including the delivery of the requested thing to the customer?
A value stream is a term that has been around for a while, but it has remained somewhat of a mystery to many people.
The truth is that a value stream is simply a practical workflow that has been used for decades.
It is essentially a way of mapping out the journey of a product or service from its inception to its delivery to the customer.
The term "value stream" originated in the manufacturing industry, specifically within the Toyota Production System (TPS) in the mid-1900s (as Michel Baudin documented).
It refers to the end-to-end process of creating a product or service, from raw materials to delivery to the customer, with an emphasis on identifying and eliminating waste.
The concept of value stream mapping was later developed as a visual tool to help identify and analyze the flow of materials and information through a process, enabling organizations to improve efficiency and reduce costs.
Value stream mapping has since been adopted by various industries, including healthcare and software development.
😱 Status: statements about processes services but no understanding on value streams.
The escape jumping on "The new shiny thing". No readiness for any maturity level (zero).
The USM Service, processes
Process model
If we test the 'processes' from all current frameworks, standards, and reference architectures against these 10 requirements, it can be demonstrated that they all describe combinations of people, process and technology: the what, the who and the how.
Therefore, they all fail the very first of the 10 requirements.
They actually describe practices, and practices are not processes: practices are derived from processes by adding the who and the how to the what. ...
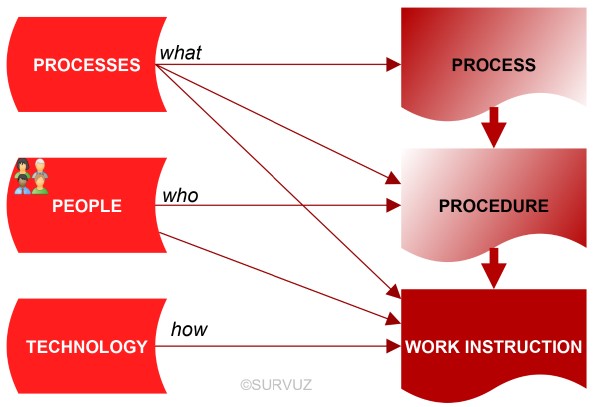
The difference between:
⚖ processes
⚙ Procedures practices
⚒ Work instructions
The detailed descriptions in different aspects for diffrences is more clear in a figure (see left side).
Confusion:
Most "processes" are internal affairs for the service provider, and as such, they are only part of the customer-facing processes.
🤔 Using this we can focus on avoiding the confusion.
What is not core value, overengineering
The Disaster of Naming Value Streams.
By definition:
- Value streams deliver direct value to the (organization's) customer
- That leads to value ($'s) flowing back to the organization
- There is only one judge of value: the customer. The one who pays for the value
Because of the above:
- A value stream is always triggered by the customer
- A value stream ends with the fulfillment of value to the customer
- A value stream always has an overlaying customer journey to it
Everything else, either:
- Supports one or more value streams, in which case it should be made as efficient as possible, or
- Is extra work, in which case it should be eliminated or justified and then minimized
A value stream is one of the most important components of an organization.
Being labeled as a value stream is not an ego play.
You don't need to be called a value stream:
- to think of and improve flow in your process
- to think end-to-end, and not functionally
- to use concepts and practices of TPS (lean)
- to use measures like flow efficiency in the work that your team does
Disagreeing with the above is like saying, "I am not working in a value stream?
Well, then I cannot focus on the customer right now because I have a product prioritization meeting to go to."
Value stream delivery needs a high degree of customer orientation and a relentless focus on execution
That is why, value streams are only customer value streams.
Focus on them can make an organization work like an elegant symphony or a Formula 1 team
Let's not create clutter and call anything else a value stream
That will just diffuse an already minimal focus on the customer
And it will be a disaster because it will ruin a simple and perfectly useful concept of value stream management
😉 Using this we can focus on the core values.
Everybody his own strategy
True Noth
When every team starts to make their True North ...
You end up, in the same organization, with:
- True North
- True North East
- True North North West
- True East
- True South East
- True South West
- True South West West
- True West
- True Up
- True Sideways
- True Parallel
- True Rear
- True Left
- True Inward
- True Somewhere
- True Oblique
- True Counterclockwise
- True Downstream
- True Right Here
- True Nowhere
Just because there is a nice-looking template, does not mean it is the right template to use.
I have seen enough product teams that have their true-north, strategy, and roadmap, with no or superficial alignment to the organizational strategy.
There is only one organizational strategy that every team, function, and person aligns with and delivers on.
There is no independent product strategy, IT strategy, Ops strategy, etc.
Organizational strategy is not a roll-up of functional, product, and country strategies.
There is an organizational True North. Everyone aligns with that.
There is no further directional clarity that every team needs to create.
There are only organizational customers, that everyone serves.
There are no internal customers, interim customers, or customers of customers.
Magnetic fields are invisible, but they can be observed through the motion of iron filings when in the presence of a magnet. The lines formed by the iron filings illustrate the magnetic field lines of force
That magnet for an organization is customer value streams.
Create alignment, and focus by organizing around customer value streams and managing through customer value streams.
😉 Using this we can focus on avoiding the confusion.
To go to a destination you must know tue North or true South where you are, what the destination is and what the possible routes are.
⚖ M-1.4.4 Strategy execution with insight
Do it correct the first time
hit an run? (A.Nesbitt)
I used to buy into the common wisdom -- that strategy is straightforward, and execution is where you hit the wall.
However, that perspective was completely overhauled when I had the chance to lead a strategy engagement for a major Japanese automaker.
What I expected to be a three-month sprint turned into a nine-month marathon.
Yet, when it was time to hit the ground running, they were off like a shot, smooth and efficient, akin to a finely tuned orchestra hitting every note.
An American CEO, one of the first to steer the US division of this automaker, explained it to me this way:
- In the Western business hustle, it's often a race to action decide now, figure out the fallout later. ...
-
The Japanese method works differently.
It's a broader, deeper dive into planning, weaving strategy and execution together.
It's not just about making a list of to-dos;
- it's about shifting 'execution' issues up front,
- tackling uncertainties head-on,
- resolving conflicts early,
- and aligning the team from the get-go.
- ... figure out the fallout later.
But this 'Ready Fire Aim' approach can lead to chaos and misfires in execution.
It's like knowing where you want to go but running with your shoelaces untied.
In most Western companies, leadership has little patience for such thoughtful deliberation and is often critical of people who do.
The cost of that impatience is high; tough, sluggish, and costly execution phases.
In short, if strategy execution feels like a Herculean task, it's likely because your strategy and plan haven't been fully baked.
🤔 Using this we can focus on how to avoiding effects by cultural behaviour.
Source of the images, allaboutlean.com C.Roser:
Do it correct by design
Dark Lean, Dark scrum, Dark Taylorism
In order to do good lean, we need to understand why some lean projects are bad.
Or, in order for practitioners to reach the light side of lean, they need to understand more about “Dark Lean.”
Just like lean, Scrum, done correctly, can yield quite some benefits in project management.
Also just like lean, Scrum can be misused.
How good intentions turn into bad attitudes:
- Dark Scrum:
is the use of Scrum primarily to put pressure on the programmers or developers.
Rather than improving the product or software development process, (Dark) Scrum is used to push for deadlines and to micromanage the developers and programmers.
Rather than quality, the focus is solely on cost and time.
Anything that can be counted counts (i.e., cost and time), and anything that can’t does not count (quality, creativity, motivation…).
- Dark Lean:
A very similar situation can happen with lean manufacturing.
The pretense of lean can be misused sorely to push on cost and time.
Pressure is piled on the worker to work faster and better, without actually improving their workplace.
Lean is used as an excuse to fire people.
Rather than improving the processes by reducing waste, unevenness, and overburden (muda, mura, muri), the focus is mostly on cost.
Avoiding the dark approach, avoiding the bad experiences of dark approaches.
Similarly, nowadays you can find quite a few people who see lean as a modern form of Taylorism, used to exploit the workers.
I have been to quite a few plants where the word “lean” was burned and refused by operators based on prior experience.
Changing the mindset of the operators toward the benefits of lean is hard. Hence, try to avoid this Dark Lean as much as you can, and bring the people to the light.
Sorry for sounding like a preacher…
M-1.5 Sound underpinned theory, foundation
Knowing the position situation in by observing several types of associated information .
These are:
- Art of the role by observed input and results
- Art of the role by follow up interactions
- Kind of task in the process by role
Non trivial means it will be repeated for improved positions.
Command & control needs information for what understanding what is going on.
Without knowing the situation or direction there is no hope in achieving a destination by improvements.
⚖ M-1.5.1 Information processes basic lean requirements
Understanding, misundertanding lean
In the understandable logical lean 9-plane proposal:
- In the centre have a goal, there are also threats
- Three pillars, a/ people b/ technology /c process
- At each pillar simplicity is at the bottom, master of art at the top
- where to start?
At the bottom right side. For all levels of the goal something must be measurable at all levels (closed loops) when you want to see the effect of wanted improvements.
- How to proceed?
Go clockwise around in a cycle verify what is going on continuously.
- From right to left at the bottom (pull)
- Followed by left to right at the top (push)
In a figure,
see right side.
⚖ M-1.5.2 Ideas from an anatomy, routes by maps, usefulness
Awareness of positions
Leaving the industrial age and going into the information age is expecting more power at the edges, needing awareness of position and situation by stakeholders.
- 💡👁❗ Geo-mapped roles idea: defining the organisation
Goal: helping organisations in the mapping of what they are doing using the generic cubicle.
Activity: the high level abstraction of the cubicle making more relevant in their business world. Customization for the position awareness is needed.
- 💡👁❗ persons ⇄ geo-maps idea: organise who is who in geo-mapped roles.
Goal: helping organisations in organising, clearing up accountabilities responsibilities for persons and roles using the customized cubicle.
Activity: Using the customized cubicle with names helps in to see the need for understanding and recognizing the logical counterparts.
A person can be named at many roles. For very big organisations this will be hardly the case, at start-ups with a very few persons the same person, name, will popup everywhere.
These two ideas are understandable business cases, achievable opportunities.
Awareness of the orgnisation system and the components
Awareness of position and situation by stakeholders and having a power for decision at the edges opens new challenges for helping organisations.
In the information age there is a shift in powers.
The required communication for defining sharing the expectations and goals clear is not easy.
- 💡👁❗ Communication flows idea: useful interactions, understanding.
Goal: helping organisations defining master data, the mapping of a shared vocabulary, language in aspect of the customized cubicle.
Activity: There are preferred ways in how to communicate with logical counterparts and what language and/or visuals are positive for achieving effective results.
- 💡👁❗ Profitability flows idea insight for: value streams, theory of constraints.
Goal: helping organisations in a mindset change to accept the new change approach.
Activity: Constraints, waste, missing respect for people, insufficient information's by closed loops are improvement options are issues to discuss and solve.
These two ideas are understandable business cases but are with uncertainties by the impact for the required changes in mindsets. Unlearn learn is hard.
Changes at the floor level for processes
The 1/2 process floor is the operational value stream serviced by the foundation 0/1.
Doing a change at foundation for execution is requiring:
- Coordination in why and what to change.
- Coordination in how to change.
These are different steps in non-trivial systems where safety continuity is important.
- 💡👁❗ Technology changes idea: improve functionality with profitability.
Goal: help in understanding the assembly line and how to optimize this.
Activity: Focussing on the operational assembly machines the technology that is used.
That technology can be improved by the way they are used or being replaced for other options.
- 💡👁❗ Safety changes idea: improve safety not hurting functionality.
Goal: good practice safety, cyber security, in a risk based value setting acknowledging mandatory legal obligations for the whole local organisational system.
Activity: When focussing on the assembly part of operations machines technology is used. Cyber security, the safety of using technology can be improved.
The assembly part is not the only that needed to be safe but the risk are very likely different.
Segmentation in the important lines in the customized cubicle should give help in strategic decisions.
These ideas are business understandable but when going for realisations will get into manage challenges at more complex situations to get solved.
Opportunities for the methodology of doing changes, how managing products
Leaving the industrial age and going into the information age is a direction with a overwhelming number of products and each of those products can be overwhelming in the number of components with specifications.
A system that is capable of managing that all is a missing link. A start is describing what it should do.
- 💡👁❗ Portfolio registration idea: Have a portfolio with product specifications.
Goal: Help organisations in documenting understanding the the products in their portfolio by the specifications of the products.
Activity: Getting an inventory of the value streams and reverse engineer the product for understanding what the intentions and specifications are.
- 💡👁❗ Managed Portfolios idea: use a tool, product that manages the complete product lifecycle.
Goal: Help organisations managing the changing portfolio from suggestions, backlog, to requirements, to validations to specifications.
Activity: There is no product in the market for this.
There should be created a standard for the product structure in the complete lifecycle so all activities are easy understandable created while the needed documentation is created with minimal effort.
These ideas are goals organisations are searching for, have a desire for, but by not being available in an easy understandable way.
Everbody is getting lost in isolated partial siloed approaches.
⚖ M-1.5.3 Process foundation, the fundaments basic creation
Getting the basics by drivers
The Secure Information Management Framework (SIMF) initiative.
Start
ask: what you can do for technology.
You must construct your technology in a way that reduces risks to the information it processes, bringing them down to an acceptable level.
And that starts with understanding the information, not the tech. and
Why Information Security Starts with Information : effective information security begins with understanding the information itself. ...
The owners of information are the business functions that create and use it.
Initiation by an entrepreneur
In the beginning there is nothing, only a vision with an idea for a product, how to control:
- processes, the way products services are created
- machines, technology that are needed
- people acting within the processes using technology
In a figure:
Foundation for information processing, expected stability
When the vision for the product is information technology related, the three categories are having a standard state by best practices.
In a figure:
⚖ M-1.5.4 Information processes controlled evaluated changes
SIMF the foundation for inforamtion processing
The foundation is influenced by many drivers. Reactive reactions in attempts to follow is what is only possible.
This type in the dimensions is not ready to be agile or do proactive actions.
In a figure:
viable system model (ViSM), viable systems approach
I hesitated connecting observations, signals direct to a process cycle.
My belief was that only consciousness decisions from a central point are valid in a system, however, for an autonomic system in viable system this is valid.
A
viable system is any system organised in such a way as to meet the demands of surviving in the changing environment.
One of the prime features of systems that survive is that they are adaptable.
The VSM expresses a model for a viable system, which is an abstracted cybernetic (regulation theory) description that is claimed to be applicable to any organisation that is a viable system and capable of autonomy.
The model was developed by operations research theorist and cybernetician Stafford Beer in his book Brain of the Firm (1972).
Together with Beer's earlier works on cybernetics applied to management, this book effectively founded management cybernetics.
The first thing to note about the cybernetic theory of organizations encapsulated in the VSM is that viable systems are recursive;
➡ viable systems contain viable systems that can be modeled using an identical cybernetic description as the higher (and lower) level systems in the containment hierarchy (Beer expresses this property of viable systems as cybernetic isomorphism).
There is more to state:
- An organic system has autonomic nervous system.
The technology environment services are expected to act like an autonomic system.
- An autonomic system needs to be taken care for.
For the needed functionalities there should be the capacities and capabilities.
- It is possible to stress an autonomic system in a way it will become dysfunctional
SIMF the foundation antipode, controlled change.
When C&C gets more mature there are options in proactive start activities in risk evaluated changes.
This is a complete different dimension than the reactive one, it ignores operations and the product development, in between.
In a figure:
M-1.6 Maturity 0: Strategy impact understood
From the three PPT, People, Process, Technology interrelated areas in scopes.
- ❌ P - processes & information
- ❌ P - People Organization optimization
- ❌ T - Tools, Infrastructure
Only having the focus on others by Command and Control is not complete understanding of all laysers, not what Comand & Control should be.
Each layer has his own dedicated characteristics.
⚖ M-1.6.1 Determining the position, the situation
People Process Technology
❶ The everlasting software crisis in the news:
Is The 60-Year-Old 'People Process Technology' Framework Still Useful?
Virtually every business leader has used the popular People Process Technology framework to help manage change in their organization. Its roots date back to the early 1960s when business management expert Harold Leavitt developed his "Diamond Model".
A framework representing the interdependencies among four components present in every organization: structure, people, technology and tasks.
The model represents that changes to one component will likely affect the other three. So, for change to be successful, the business must evaluate and manage the impacts across all four areas.
... the components most commonly used today: people, process and technology.
That is a strange limitation, reduction to review.
Those three are the ones managed by command & control and ignoring command &control (structure) ignoring the C&C itself.
Leavitt
dealt with the analysis of patterns of interaction and communication in groups, and also interferences in communication. He examined the personality characteristics of leaders. He distinguished three types of managers:
- The visionary and charismatic leader is characterized by being original, witty, and uncompromising.
He is often eccentric and seeks to break with status quo, and embarking on a new path.
- The rational and analyzing leader is holding to the facts supported by numbers.
He is systematic and can effectively control.
- The pragmatist - The contractor of established plans, skillfully solving problems.
Leaders of this type are typically not visionary.
A more structured review:
E-government Designing IT Operating Model for Managing IT Services (Hamdi Riady, Nur Sultan Salahuddin - aug 2019 )
🤔 Structure and approach of C&C to involve in retrospective.
Context confusing: business - cyber technology
❷ There is a lot of misunderstanding between the normal humans and their cyber counterpart colleagues.
Not that cyber people are not humans but they are using another language, jargon, in communication.
That culture of misunderstandings is not necessary and should be eliminated.
🤔 A translation of words to start:
ICT | Business | | ICT | Business | | ICT | Business |
Strategy | Control | - | Functional | Target-Value | - | Confidentiality | People |
Tactical | Orchestration | - | Compliancy | Communication | - | Integrity | Processes |
Operational | Realization | - | Technical | Information | - | Availability | Machines |
A figure:
See right side
There are several paradigm shifts:
- Leadership: "Strategy, Tactical, Operational" and "Control, Orchestration, Realisation" are both used for justifying hierarchical power.
Although that is a fit, both are incorrect. Hierarchy is just another dimension.
- At the floor: "confidentiality, Integrity,Availablity"
a good fit with: "people, Process, Machines"
- At the roof "functional, Compliancy, Technicality"
a good fit with: "Target - value, Communication, Information"
- Information : the asset "Information" is a business asset not something to be pushed off as incomprehensible "cyber".
Information processing is enabled by technology, technology acting as a service.
- Compliancy : The communication, accoutablity is placed at business context.
What is in demand by risk management considerations, to be deliverd in a service approach.
There focus is on task activies in lines to design / develop and realize / operate a product.
Out of scope are dimensions for:
- Leadership: hierachical lines of power and control.
- Time: In what a product / hierachry: was (paste) is (now) and would be (future).
- ....
❸ In the figure the cubicle bottom and top did not get context.
What could be there?
- Left side = technology (service operations), right side organisation
- front side = technology (service functions), back side processes
- 🤔 bottom people personal interests, top people group interests
⚖ M-1.6.2 Determining the destination, strategy
Strategy vs. planning -- what's the difference?
❹ Confusion in expectations and goals.
Why a Plan is NOT a Strategy
Strategy vs. planning -- what's the difference?
- Strategy: choices that position you to win.
- Planning: who does what by when.
Many organizations treat planning as a substitute for strategy.
Their "strategic plan" is just a list of projects and initiatives.
They won't lead to winning. Because they have no coherence.
The result is not bigger than the sum of all initiatives.
👉🏾 Strategy is a theory of how you win.
The few priorities that - together - are More than the sum of its initiatives.
A successful business needs both: Strategy and planning.
Mistaking one for the other or avoiding strategy because planning feels easier is a sure way to failure.
Graphic by Jeroen Kraaijenbrink
An IT strategy or an IT plan
❺ Statement: We don't need a separate IT strategy; our overall strategy is sufficient.
The reasoning:
- Information Technology (TT, ICT, ITC ) is a fundament of your organization.
- Your IT systems determine how good, efficient - reliable, your services are.
- They ensure that your stakeholders, that includes your customers, are and remain happy.
- ICT is not a goal for itself. It is a means to support and strengthen your organizational strategy.
They help you to fulfil your social mission and to fulfil your legal obligations.
🤔 That's why you need an IT plan that aligns with your organizational strategy.
The missing link is C "Communication".
An IT plan that:
- makes clear what you need, what you want and what you can do.
- helps you make smart choices, save costs and prevent problems.
An ICT strategy or a ICT service plan
❻ A general ICT strategy, on the other hand, is possible, but that will be a completely different world than the current ICT.
The big difference is: focus on Technology vs focus on Provision as a Service.
If you don't do anything with your strategy, you might as well not have a strategy.
It only costs time, in the end it doesn't yield anything. Hoshin Kanri: a few nice A4 sheets with some text.
"There is nothing quite so useless, as doing with great efficiency, something that should not be done at all." and "Culture eats strategy for breakfast." (P Drucker)
The goal of a strategy
🤔 A reference to a checklist:
what is good strategy often not easy to activity (2024)
A good strategy must first envision what the world will look like in the time frame you are aiming at, 5 years, 10 years, 15 years, etc. then the strategy must envision what the needs will be at that time.
Then a good strategy will understand the major technology, world order, and group think trends at that period. It goes way beyond good planning.
There is a misleading trend going on that says that strategy is separate from futurism. They are intertwined. The naysayers continue by saying that nobody can see the future, which says that Dick Tracy, Startrek, and 2001 A Space Odyssey never happened. The data points and trends are all around us, just not the precision.
Tradional strategic planning that extrapolates on yesterday’s strengths and weaknesses is useless and dangerous in an exponential world. (Bill McClain)
Here are 9 pointers to get you started.
❼ Where to start and how to proceed for these 9 pointers in the figure by their positions is unintended a good fit for the SIAR model that extended into Lean understanding.
⚖ M-1.6.3 Managing Uncertainties, confusion, ambiguities (MUCA)
Misunderstanding by missing standards
❽ The complexity in the volatile world has a root cause in disorder and muddle.
What is felt als comlexity is simplified by solving confusion (state of being bewildered, unclear).
To solve are the mentioned examples:
- What is "a service"? (what)
- What is "a process"? (how)
- What is "the value stream"? (where)
- What is "data"? (who)
- What to do with "requirements"? (when)
- What are the "specifications"? (which)
State of art architecture: requirements
Togaf: requirements
The most used framework for enterprise architecture as of 2020 that provides an approach for designing, planning, implementing, and governing an enterprise information technology architecture.
It is typically modeled at four levels:
- Business,
- Application,
- Data,
- and Technology.
It relies heavily on modularization, standardization, and already existing, proven technologies and products.
When looking what it is about, it is requirement management by a framework and dictated by tools.
❓ Does this help for:
- The value stream.
Only external customer / stakeholder
- Translating a vision into missions.
Context for missions to realizations.
- Organisation awarenees: anatomy, route by maps
❌ All of this is missing, it is about requirements in a big design upfront.
No agility in doing only those when clear enough during the journeys.
⚖ M-1.6.4 Ambiguity in dimensions: foundation floorplan
Building a foundation floorplan
❾ The floorplan is build by levels, the start:
- the promise of a product with value being delivered.
- a short term vision has popped up reactive based on socio-cultural and political/regulatory drivers.
- a long term vision is awaiting being proactive based on socio-cultural and political/regulatory drivers.
- the promise of a product with value being delivered.
Connecting those two directly is missing a lot.
There is some feeling of energy and a goal but not seeing those essential parts for information.
😉 Building up the floorplans there is a goal for usage by customers and workers:
- There are routes to investigate in the anatomy what is shown.
- We can find where the processing to be done is located.
- Someone possible held accountable is findable of a product with value being delivered.
Using the foundation floorplan, roof layout
❿ Milestones: Understanding the geo-mapped roles and who is who at those.
👉🏾 Milestone: The foundation floorplan has grown to be usable for the planned construction.
In the context of an organisation:
- The vision is clearly defined, explainable realistic.
- In the dimension of stability a minimum viable set of technology requirements are defined, explainable realistic.
- Being ready for operational activities expected conform missions as a result of the vision.
👉🏾 Milestone: The floorplan for the future supporting change has got a minimum viable structure.
In the context of an organisation:
- Legal obligations and financial conditions are covered in the minimum viable structure.
- In the dimension of expected changes: support by changes in the external environment is covered in the vision.
- Being ready for changing operational activities expected conform missions as a result of the vision.
There are two dimensions, two different type of worlds, antipodes:
- One of stability without change.
- Another continuously changing without stability.
Only the content of physical surface is shown, the two logicals are the counterparts.
Interacting, changing between those worlds is hard.
👉🏾 Milestone: There is an autonomic system in place for the service provision technology.
In the context of an organisation:
- The expectations for the service as a vision are clearly defined.
- In the dimension of stability a minimum viable set for the technology service are agreed.
- capacities and capabilities for the service are aligned with the expectations, viable setting.
There is no generic approach that is a fit for any organisation.
👉🏾 Milestone culture: change innovation, improvements in a scientific organic lean approach.
In the context of an organisation:
- Impact for proposed changes are evaluated before they are handed over to get realized.
- The realisation stage is an iterative process during which:
- shared holistic goal although details are not clear or known.
- details are architected and designed in cooperation with closed loops.
- Building components is done with closed loop for what is clear.
- Validating components is done with closed loops for what is build.
- Impact for changed specifications are evaluated before they are handed over into a portfolio service, product.
There is no generic approach that is a fit for any organisation.
M-2 Command & Control gaps understanding and solutions
M-2.1 Seeing ICT Service Gap types
Preparing the building of any non trivial construction sould include safety.
❗Aspect:
People, safety, functioning topics are:
- high level design & planning
- detailed design & realisation
- evaluation & corrections
Non trivial means it will be repeated for improved positions.
In the digital information age a basic structure is needed how to do an realisation by stages.
Without a basic standard structure any solutions is forced to reinvent the wheel continuously.
⚖ M-2.1.1 Understanding safety, functionality by requirements
The V-model extended to a W-model
the wedge model 2
The V-Model, possibly first defined by NASA in the 1960s, repeated by Barry Boehm in 1979 and Rook in 1986, has served well as a depiction of development of nontrivial systems.
The V-model has commonly shown verification of system elements that are on the righthand side, against requirements for each element that are on the left. ...
Whilst valuable, this depiction is a very limited representation of the reality of work products created in the development of non-trivial systems, and their verification and validation relationships.
The Wedge Model extends the basic V-model to incorporate verification and validation of requirements, design, system elements and system. ...
So we have a W-model.
The original V-model has been described from time to time as a development process model.
It is not. The model shows the products of engineering work, and their problem-solution relationships, but is silent on how the work products were created.
The original V-model has also been described as a Waterfall model.
It is not that either. In showing the end-product relationships between work products, the V-model does not preclude, for any work product, a history of development of that work product.
The V-model extended to a W-model
The V-model during design & build has a closed loop between requirements and validations.
The W-model adds a closed loop between those that defined requirements for some reason with that reason and the design & build activities.
Left open:
- How to collect requirements for building.
- How the manage design & build.
- Levels in the requirements, suggestions, backlog for a product, service.
- Going from requirements to validations to specifications
⚖ M-2.1.2 Changing safety or functionality
Sources, stake holders for collecting requirements
The requirements sould come from:
- product vision missions what should get operational
- technology aspects from what is operational
- executing capabilities: changed market options
- enabling capabilities: regulations and policies
- executing capabilities: experienced issues
- enabling capabilities: experienced issues
Collecting requirements changing technology functionalities
Changing operational executing capabilities (ALC-V types) in a figure:
Collecting requirements changing safety cyber security
Changing operational enabling capabilities (logical access - safety) in a figure:
⚖ M-2.1.3 Safety technology alignment
Cyber security, generic technoloy quest outsourcing
State of security, a supplier perspective:
Microsoft Digital Defense Report 2024 Highlights:
- In all cases, we're creating "paved paths" for engineers, so that the easiest way to do something is the also right way.
- With more than 600 million attacks per day targeting Microsoft customers alone, there must be countervailing pressure to reduce the overall number of attacks online.
- In more than 90% of cases where attacks progressed to ransom stage, the attacker had leveraged unmanaged devices in the network,
- Moreover, over 70% of malicious entities are active for less than two hours, meaning they may be gone before they're even detected.
These are technical generic infrastructure components challenges.
A sophisticated security operations centre is not an option for most organisations.
A external service is an escape.
Cyber security, generic technoloy quest topics
Identities access control is fundamental for organisations.
- Encourage all organizations to commit to the foundational security principles: secure by design, secure by default, secure operations.
- A robust deterrent framework will help to: promote stability, protect critical infrastructure, avoid some of the most harmful cyberattacks.
- An attacker who manipulates identity can also manipulate any resource or process that identity is trusted to access, including email, other cloud services, or the on premises environment.
- Despite the emergence of more advanced hacking techniques, most ATOs still happen through simple methods like password spraying, phishing, keylogging, and using passwords from previous attacks found on the web.
- As the world recognizes the persistent threat of cyber enabled crime, we are seeing more public and private partners joining forces to disrupt criminal infrastructure, hold them to account, and support victims of cybercrime.
- As deepfakes become more common in the business environment, organizations will have to implement countermeasures, such as requiring additional verification for transactions.
⚖ M-2.1.4 Safety information, data, alignment
Data quality costs, information qualitye safety
datagovernance
Why don't we put more energy in prevention?
Do you realise that every organisation, with the current approaches to data spend 10% to 30% of their yearly turnover on fixing data-related issues.
Sources state: "Poor data quality costs organisations $12.9 million every year on average": (dci)
Well known issues (top) can be handled with a short term or long term vision.
See right side
Information safety, principle least privilege
Granting access by roles requires an good understanding of all functionalities by roles.
A person can have several roles for activities and activities with functional restrictions.
There is a "Devil´s Triangle" on its own wiht IAM. Conflicting types of interest:
- Giving granting access to humans. Conforming the hierarchical organisation structure.
- Securing technical systems, the supply chain included. Conforming compliancy.
- Design secure Platforms, secure organisational business information processes.
A figure:
See right side
👓
click on figure for modelling the relationships and building realizations.
M-2.2 Floor plans, seeing value streams
Building any non trivial construction is going by several stages.
❗Aspect:
Machines, technology topics are:
- high level design & planning
- detailed design & realisation
- evaluation & corrections
Non trivial means it will be repeated for improved positions.
In the digital information age a basic structure is needed how to do an realisation by stages.
Without a basic standard structure any solutions is forced to reinvent the wheel continuously.
⚖ M-2.2.1 Standard patterns information flows, process changes
Business applications, what is?
❶ A
business application is defined by:
- Composed of two complementary components.
- Information at the value stream seen materialised as data.
- Transformations of information in the value stream.
- Materialised data is seen at some type of storage.
- Transformations are processed by tools, platforms.
- Covers the value stream for customers and
all related activities, documentation, registrations.
Business applications, transformation types
❷Three types of business applications transformations:
- ALC-V1 A process that is run once.
When after each run many adjustments are needed, then it is also a one-off.
- ALC-V2 processes with transformations are based on rules set by human decisions.
Processes are repeated many times without change. A change in processes is versioned with specifications.
Development and verifications is done with fake, synthetic information.
❗ Only the production environment uses operational information.
- ALC-V3 processes are based on what is seen in the operational information and what is known by operational examples.
Processes are repeated many times without change. A change in processes is versioned with specifications.
Development and verifications are done with operational information.
❗ All environments are using operational information.
Segregation between the stages is important but not the same as at ALC-V2.
Business applications, context
❸Two contexts of business applications:
- Running operating the value stream mapping process, VaSM
- Changing the value stream process within a viable system model, ViSM
⚖ M-2.2.2 Information, process flow - change flow
ALC-V3 Information flow by four stages
The push line, the pull line is not there.
❹Using the operational value stream, supporting by at least a validation line, in a figure:
ALC-V3 Process change control by four lines
The push line, the pull line is not there.
❺Changing the operational value stream, supporting by at least a validation line, in a figure:
⚖ M-2.2.3 Processing information vs industrial differences
The dark side of trying to industrial approaches
There are many attempts to operate information processing like industry.
Understanding the value stream, goals by missions are not in place.
❻ Ideas for root causes:
- It is not creating a product to consume or use, but a service.
Examples showing differences:
- A car is product with the personal transport as goal.
- Food are products with the personal consumption as goal.
- Registration of a legal right, insurance, banking, property ownership, promise of future delivery, are services.
- Information registration by itself is the fundament in doing the service.
Differences by impact in ownership:
- A product owned may get destroyed, consumed, by the customer owner of the product.
- An agreed service may get adjusted sold, initiated by the customer but the owner of information registration is the service provider.
Why the customer cannot control the information registration freely is clear when it is a banking account or property ownership.
There is a lot of confusion for the information ownership and the "privacy" rights.
- In the industry a hierarchical control to manage actions to the detailed level was normal.
When processing information that hierarchical control is the problem.
Micromanagement is blocking the working force.
Decisions by hopium are not solutions solving missions.
Closed loops during processesing, avoiding the "defects".
Monitoring what is going on is about quality, quantity & impact.
Closed loops within the operational value streams should be in place.
❼ There are several points (7,8) to do validations:
- input information is made usable, after Staging
- information is prepared to process, afer Semantic
- result information is ready to deliver, afer Databank beore delivery
Closed loops on value stream results.
❽ The goal is results conform the mission goals (6,9).
- A defined safe state when the outcome can have an impact to avoid when that result is false.
- At a high vital service an additional flow evaluating new options before changing is needed.
- From the total population the impact for all relevant subgroups should be part of the design.
- Changing process flows is done by changing orchestrated four dependent process activities in the standard pattern.
Adding features following the flow, removing them, backwards.
⚖ M-2.2.4 Using the portfolio management system Jabes
Portfolio Process: usage, demand & delivery
❾ Goal: The information transformations known & in control by all their asspects.
Craftmanship, deliverables & validations:
◎ ⇄ | reviewing: verified: information maturity levels (independent) |
◎ ⇄ | reviewing: quality of information results delivered & expectations |
◎ ⇄ | reviewing: quantity of information load delivered & expectations |
⇄ ⇆ | Planning and balancing alignment, the complete value stream |
⟳⇅ | Evaluating solving operational issues at processes & technology |
⟳⇅ | Evaluating solving expected capacity issues for processes & technology |
In a figure:
See right side.
Portfolio Process: ideate, initiate & technology validation
❿ Goal: The change processes known & in control by all their asspects.
Craftmanship, deliverables & validations:
◎ ⇄ | reviewing: verified: processes maturity levels (independent) |
◎ ⇄ | reviewing: quality of processes results delivered & expectations |
◎ ⇄ | reviewing: quantity of process load delivered & expectations |
⇄ ⇆ | Change and innovation alignment, following and/or initiating |
⟳⇅ | Evaluating Proposals innovation & changes for processes & technology |
⟳⇅ | Evaluating Proposals expected capacity load for processes & technology |
In a figure:
See right side.
Information process portfolios, a cultural mindset
The value stream has mandatory requirements to be fulfilled be specficiations for the products, services in the portfolio.
As long the product is relevant, that is customers are using it or are able to refer to it, the information of the portfolio product service for dedicated version should be at least retrievable.
To get covered by information functional knowledge by a portfolio:
- Systems deliveries architecture
- Safety, security architecture
- Systems product flows architecture
- Information understanding master data
M-2.3 How to steer in the information landscape
Managing operations in any non trivial construction by stages.
❗Aspect
Processes topics are:
- high level operations & planning
- detailed operations & realisation
- evaluation & corrections
Non trivial means it will be repeated for improved positions.
Managing the process, information is needed for understanding what is going on.
Without knowing the situation or direction there is no hope in achieving a destination by improvements.
⚖ M-2.3.1 Strategy learning, improvements
Tools Strategy mind mapping
Evaluating thinking on what to do is not easy.
do you know when to use what strategy tool
Do you know when to use what strategy tool?
There are 100s of strategy tools out there.
Most people make 1 of 3 mistakes:
- Use the same tool every time.
- Skip them altogether.
- Overanalyze everything.
But how do you know which one to pick?
You don’t need to do any of that.
Think of strategy as a response to the challenges blocking your goals.
First step: Identify your challenges.
Then, focus only on those.
Here's some orientation:
(M Sniukas)
Strategy development
A.Nesbitt,
it isn't a straight line. It's a loop.
Most people make a huge mistake when they use the Play to Win framework for strategy.
They treat it like a linear process to answer the key questions:
- What is our winning aspiration?
- Where will we play?
- How will we win?
- What capabilities must be in place?
- What management systems are required?
They start at the top and work their way down the list without any learning loops.
Even worse, they treat it like a hierarchy, where bosses answer question one and pass it on to the next layer, and so on.
The figure is presented as a waterfall, but clearly a doozy mistake to interpret it that way (dark pattern).
⚖ M-2.3.2 The practical Value stream map, VaSM
VaSM events, Warehouse Management System. (WMS)
The abstraction of a value stream is very generic.
Events are marked by a date-time stamp. At summarisation level for management information a date stamp is sufficient.
Challenges:
- The technical representation for data, date-time are not standardized.
- The goal and usage of an event is not standardized.
- What events are important in the value stream is not always clear.
- Stakeholders in partial processes not speaking the same language.
Searching for what has been done:
Assessment of the implementation of a Warehouse Management System in a multinational company of industrial gears and drives
The focus for that paper is the WMS (software system) and not the manufacturing or sales flow. It is nicely showing the events and linear steps controlled by four different departments (stakeholders).
A figure:
See right side.
(Rafael de Assis, Juliana Keiko Sagawa, 2018)
VaSM events, full cyle abstraction
Added in the pull line: sales and intake process.
The clokcwise lineage is:
- IV The pull request, initiated at the right (basket pull)
- IV-III Verifying requests on conditions (reject) before produce at the bottom
- III-I inbound warehouse preparin collection external & internal materials
- I-II Manufacturing with quality check (push) at the top
- II-IV Delivering using possible multi channels at the right, outbound warehouse
A figure:
See right side.
⚖ M-2.3.3 Defining, analysing the value stream
Value stream mapping tool support
Support for VaSM using visio (Microsoft).
You can use Visio to create value stream maps, with current state and future state diagrams, to identify where there is waste in manufacturing processes, and to help find ways to eliminate that waste.
There are multiple issues:
- This figure for VaSM only gives attention for the assembly activities.
That is only 12½% off al the area's of the full cycle.
- The note states only looking for waste, that is very small part of what real lean is about.
Jumping for tools and by that not having in mind the full process cycle of the value stream is awaiting for failures in improvements.
Value stream mapping framework support
The scaled agile framework
SAFe did only focus on software deliveries in a top down micro-managed way.
A change in that in (2024) adding VaSM and customer centric.
Pitiful it are only notes missing the impact of the concepts of values stream and lean.
Value stream understanding grouped events
Process mining is reverse engineering the value stream (VSM).
From: "Want to do a process mining project"
slides and videos (vdaalst).
❗ Get information of the expected possible flows, for example.
Several sequential process flows in a figure:
See right side
Grouping: "place order", "send invoice", "pay" to one action (IV) . "make delivery", "confirm payment" (II) to one action and add the assembly (I) simplifies to the four basic steps.
⚖ M-2.3.4 Getting value from the value stream
What is VaSM, the scope in definition
THe scope of what a value stream is, is important:
VaSM customer
Value Streams are only customer value streams. For 2 key reasons:
- "Customer" is only the organization's customer.
Gives the organization value to survive.
Pays the organization's salaries.
- Value is determined only by external customers.
Internal customers determine what is "valuable" to them.
That need not mean value to the customer.
It is a fallacy that if everybody internally gets value, that will lead to value for the customer.
Thinking that if every function is efficient then the whole organization is efficient, is illogical.
If you want to drive excellence in your organization, manage your organization as a cluster of value streams and subordinate everything else to those.
That is the only way to have the highest efficiency, effectiveness, and sustainable future for the organization and the staff.
Reactions:
-
Most of what we seem to be thinking about As value streams are not customer value streams, but are internal process workflows, which are at a lower level of abstraction.
(Pete Nathan)
-
Refers Jim Womacks presentation.
He mentions numerous times how in most organizations they can't even identify what their value streams are ...
(Doug Rabow)
Take the Value-Stream Walk Presentation by Jim Womack (2011, lean enterprise institute).
purpose, process, and people as the keys to implementing and sustaining a true lean management system.
The reason: Managers and executives must learn to think "horizontally" across functions in order to understand and improve the flow of value to customers.
This means un-learning the traditional "vertical" thought process based on organizational charts and optimizing departments.
What is VaSM, the scope in definition
great strategists are rarely great planners
Strategy and planning, while closely related, require fundamentally different mindsets and skills.
- Great strategists are rarely great planners.
- Great planners are rarely great strategists.
Success demands both visionaries and organizers.
The challenge is recognizing and respecting these as important but different skills—and likely resident in different people.
Weaving these two groups of people into an effective team that works well together to produce results is where leaders need to earn their pay.
M-2.4 Roles tasks in the boardroom
Managing the working force at any non trivial construction is moving to the edges.
❗Aspect:
Communication, cultural changes are:
- Trusting the working force while getting also well informed
- Respect for people, learning investments at staff
- Accepting uncertainties and imperfections
Non trivial means it will be repeated for improved positions.
Managing the working force at processes, information is needed for understanding what is going on.
⚖ M-2.4.1 Changing role C-level
Servant leader
how to accelerate-your strategy execution (2024)
The concept of servant leadership is a valuable approach to enable your organization to execute its strategy.
Servant leaderschip, the only cheat sheet you need:
Without knowing the situation or direction there is no hope in achieving a destination by improvements.
⚖ M-2.4.2 Steering changing roles (I)
Chief Revenue Officer (CRO)
What is a Chief Revenue Officer (CRO)? (LI sales solutions 2024)
They're under pressure to understand what their customers value now, how their talent will be impacted, and how to reprice for this inflationary environment.
Just like consumers during times of record inflation, CROs will have to be careful with spending.
Sellers need to provide clear visibility of ROI to help them make confident buying decisions.
But this uncertain climate is also an opportunity to bring clarity to CROs.
As they look to minimise the impact that macroeconomic changes have on their revenue, they need solutions that drive steady growth now and in the future? solutions that you may be able to deliver.
CROs act as the cornerstone that brings together siloed teams with a shared goal and provides the vision, tools and processes they need to stay focused on revenue.
They look at the bigger picture and help bring together the strategy that guides a number of teams? not just the sales team.
And while they do focus on the money side of things, unlike the CFO, they're not responsible for accounting.
CTO Chief transformation officer
Mc Kinsey:
what does a chief transformation officer do? (2024)
The CTO role isn't a one-size-fits-all position.
The context, scope, and objectives of a transformation vary depending on an organizations needs.
Generally, the demands of a CTO can be broken down into three major categories, based on the conditions leading to the transformation and the level of change required:
- Responder
Respond to a crisis or major setback, including macroeconomic pressures, competitive threats, or shifts in customer preferences.
Responders must stabilize the business and enable rapid and substantial financial improvements by building new levels of discipline and speed, as well as capabilities tied to execution.
- Revitalizer
Act on: when a business has seen its performance degrade over time.
Revitalizers are expected to drive accelerated performance improvements with an emphasis on sustained, long-term change.
These CTOs emphasize mobilizing and empowering an organization, digging deep to rally and inspire employees for the new journey ahead.
- Reinventor.
These CTOs lead the organization through substantial strategic changes, for example, by shifting a business model from brick and mortar to digital or entering an entirely new product category or market.
Reinventors should articulate a clear strategic vision and deep focus on building new capabilities to support that vision.
These archetypes aren't set in stone.
CTOs might be asked to start out as a responder and then transition to a revitalizer.
And there are some transformation leaders who don't fit any of these archetypes.
"Reporters," for instance, are a subtype who play more of a project management role. ...
T Transformation CTO role
The same on a CTO, PEX Business Transformation Europe Summit ( october 2024).
- Understand ways to maximise technology-driven transformation and minimise the risk of data security and bias to ensure that AI can be a part of a holistic transformation strategy.
- Identify areas of transformation so that we dot not have a "one and done" mentality.
Adapt a continually evolving strategy that aligns with businesses-wide strategic objectives.
- Discover strategies for overcoming resistance to change, ensuring the whole company ecosystem feels ownership of transformation from the grassroots to the boardroom.
- Maintain a transparent relationship with core stakeholder and leaders within your organisation, not only by operating agile but by ensuring this agile approach carries through into the way we demonstrate results and ROi.
- Experiment, innovate and gain from losses.
Challenge your approach to transformational people leadership and digital strategy by learning from transformations that went wrong.
⚖ M-2.4.3 Steering changing roles (II)
The enterpise organisation, executive
When the product service is what is about, the CPO (Chief Product Officer) has a pivotal role.
A CPO is more then than the COO (Chief Operations Officer) it is including innovation (Chief Innovation Officer), technology alignment, involving empowered people.
Proposal for a abstracted strcuture:
- CFO Chief Finance officer, CDO Chief Data officer, CEO Chief executive officer
- CAIO Chief Analytics & intelligence officer, CPO , CTO Chief technology officer
- FM/HR Facilities and Humanity, CSO Chief Safety officer, CRO Chief risk officer
All of them are exchangable to other enterprise
Top-down theoretical view:
Figure, see right side
Lean Product and Process Development. (LPPD)
lppd (J.Womack 2019)
Why We Must Focus on Product and Process Development. ...
The Machine isn’t Only About Factories. ...
LPPD folks must insist that new products be developed with a lean fulfillment process – that’s part of your job.
Isn't that what the chief engineer is supposed to see to? (CPO)
And you could insist that we do product and process development simultaneously and concurrently.
"I bet you can apply this to every value-creating activity at every organization, every industry in every country. You’ll do it."
So that's what we said a long time ago.
“It’s not just product development, it’s product and process development because every product must have a fulfillment process.”
An alternative word, 3P: Production, Preparation, and Process. This goes into problem solving mostly focus on the factory, production not the product.
However, it's crucial to recognize that the 3P Process is not an elementary tool.
It demands an intricate understanding of other Lean principles and is typically suited for companies well-advanced on their continuous improvement journey.
⚖ M-2.4.4 Transforming steering roles
Pathway to an Agile Enterprise
ACOE (A Resource Library with Hundreds of Public Enterprise Architecture, Business Architecture, and Soft Skills for Architect resources. 2024)
EA Soft skill (2022)
You may know how to do Enterprise Architecture or Business Architecture, but ensuring your organization can adopt these practices requires different skills.
Soft Skills for Architects.
Over the years, we have observed that Soft Skills are just as important, perhaps even more important than hard skills.
An architect may have mastered the process, tools, and templates for developing architectures.
However, it's impossible to create architecture in a vacuum.
Without the necessary interpersonal skills, the architect will not be successful in engaging the right people, understanding their perspectives, and then building a framework that will be purposefully used by the organization.
The work of an Architect is Challenging Indeed.
It requires a robust set of analytical and organizational skills and tools.
But it also requires one to navigate an organization to find the right people, engage them in the effort and tap into their thinking and beliefs.
It requires the ability to bring together people with different views to create shared views.
Simply put, the architect must be able to lead people to be successful.
Additional links:
- Business Architecture Center of excellence: BACOE
- Enterprise Architecture Center of excellence: EACOE
Recognize the pathway to an Agile Enterprise is a pathway of change.
Enterprise Architecture illuminates how an organization and all of tis members can achieve its objectives, through the creation of a series of engineered models and project initiatives, that can be easily understood by all of the people associated with the organisation.
The enterpise organisation, executive
Complexity is aborbed where it arises, in line with power to the edge. Business within the busienss.
viable system model (viSM)
Problems should be solved where they arise.
In other words, as decentrally as possible, because that is where the best information is available and where you can react the fastest.
This is what the principle of subsidiarity tells us: problems should only be solved at the higher level when they can no longer be solved by the lower, more relevant level itself.
Delegation is, so to speak, from bottom to top instead of top to bottom.
That is also why some Chinese companies work faster and better than our own.
The Viable System Model shows us how to design the necessary decision-making structure in the company.
The basis is the correct design of the operational units in which value creation is created and the purpose of the company is fulfilled.
M-2.5 Sound underpinned theory, operations
Knowing the position, situation in by observing the floor.
❗Aspect:
Information, types of association relations:
- Art of the role by follow up interactions
- Kind of task in the process by role
- Art of the role by observed input and results
Non trivial means it will be repeated for improved positions.
Command & control needs information for what understanding what is going on.
Without knowing the situation or direction there is no hope in achieving a destination by improvements.
⚖ M-2.5.1 Simf: the complete operational flow cycle
Focus gaps in the operational value stream
When a value stream gets attention the focus is on the production assembly line.
The This is only 12½% off al the area's.
Some business models don't even use the assembly area intensive but very limited.
Trading & selling is not doing much in "manufacturing" in the flow.
❓ Why just that limited focus on a small part of the system?
- It is a technology driven mindset area, easy to delegate, easy start.
- It avoids those more difficult challenging part of plannings:
- long term planning by command & control
- mediate term planning for purchase, manufacturing, construction operations
- short term planning for customer deliveries, customer interactions
SIMF the foundation for information processing
A full complete generic value stream flow in a cycle with a pull-push in a figure:
⚖ M-2.5.2 Simf: the complete desing & build flow cycle
Focus gaps in the opeational value stream
When the change for a value stream gets attention the focus is on coding.
The This is only 12½% off al the area's.
Some business models don't even use the coding because solutions are purchased.
When doing business running business in a mature commodity market there is no real differentiator by better code without doing disproportional investments.
❓ Why just that limited focus on a small part of the system?
- It is a technology driven mindset area, easy to delegate, easy to start at.
- It avoids those more difficult challenging part of:
- Defining the requirements tot work at in a clear understandable way limited at a high level to what is needed for design
- Form the limited requirements at a high level what should cover the design architect and engineered more detailed one enabling the realisation
- An organized structure for: design, development, validation cycle line in the standard engineering "V-model" for creating products, services.
- Validating new services & products deliveries into specifications by functionality
- Validating new services & products for compliancy, safety
SIMF the foundation for information processing
A full complete approach for creating & changing value streams in managed suggestions, backlog for requirements in a cycle with a pull-push in a figure:
⚖ M-2.5.3 Realisation, control & command dimensions seen outside
SIMF the processing for realisations, outside view
Just reversing inside outside view vice versa reverses the experience inleft and right.
This breaks a simple copy paste of the cycle flows seen at floorplans.
👁 Operational processing flow and the changing of the operational processes is right to left.
👁 Suggestions, ideas proposals for improvements are in a flow going bottom-up.
The complete area of information processing in a figure:
SIMF the processing for realisations, outside view
Industrial age: the manager knows everything, workers are resources similar to machines.
Information age, required change: a shift to distributed knowledge, power to the edges.
👁 Operational processing flow and the changing of the operational processes is right to left.
👁 Suggestions, ideas proposals for improvements are coming in at the top going top-down for optional start of creation and change activities.
Left open is how ideas proposals are collected, managed. In a figure:
⚖ M-2.5.4 Antipodes in Simf and maturity levels
Purpose dimension, the vision
The antipodes are seen by the difference at the foundation floor (0-1) and the top floor for controlled change (3-4).
The axis is the vertical but neither of these floors has a clear ordering by some change or control cycle.
In the middle there is a duplication caused by the topple point.
- design & build the operational process ⇄ run the operational processes
- The information warehouse backend ⇄ The information warehouse frontend
- Knowing the customer at demand ⇄ Knowing the customer at delivery
Managing and processing dimension, People
The antipodes are seen by the differences for processing by workers and the administrative managing actvities.
The axis is a horizontal but the middle has no clear defined topple point.
It is about people their mindset, skills, education and social environment.
In the modern times that is for an enterprise external, in the defence setting it is internal.
Managing and processing for the purpose, missions
The antipodes are the side of control & command and the realisation in information processing.
The axis is a horizontal one with levels at the vertical
- (0-1) reactive, "best practices"
- (1-2) managed operational value streams (VSM-s) in processes
- (2-3) able to create & change controlled the operational VSM-s
- (3-4) pro active changes at information processing
- (4-5) influencing the purpose for information processing
M-2.6 Maturity 3: Enable strategy to operations
From theoretical to practical needing the collaboration.
❗Aspect:
Purpose, value, interrelated areas in scopes:
- ✅ P - processes & information
- ✅ P - People Organization optimization
- ❌ T - Tools, Infrastructure
Only having the focus on others by Command and Control is not complete understanding of all laysers, not what Comand & Control should be.
Each layer has his own dedicated characteristics.
⚖ M-2.6.1 Short term results or long term results (I)?
The Danger of Short-Term Thinking
❶ The gold rush, silver bullet, hopium for miracles.
FTSR Ed.28:
Focus on Outcomes or Face Failure
Let's face it: short-term wins might give you a quick high, but they won't build lasting success.
If your focus is only on hitting the next quarter's numbers, you're setting your business up for failure.
Real strategy is about having a broader perspective on long-term thinking. Here's why -- and how you can start doing it right.
Focusing on quick wins feels satisfying at the moment, but if that's all you do you will sabotage your long-term goals.
It's easy to get caught up in chasing that next target, but when those short-term victories take priority over sustainable growth, you're walking a tightrope.
If you're not looking beyond the next quarter, you're already losing.
Shifting to a Strategic Mindset
Stop worrying about the next few months. The decisions that influenced the success of the near term were taken months ago.
Escape the rat race and start thinking about where you want your organization to be next year, in 3 years, maybe even in 5 years.
Thats where the real work starts. Set longer-term goals that guide your team's decisions and create alignment around a vision of future success.
Your strategy needs to reflect that vision in every move you make.
How to Balance Short-Term Wins with Long-Term Success
❷ The bigger purpose as vision.
Here's the reality: short-term wins matter but must serve a bigger purpose.
Use them to build momentum, but don't let them distract you from your long-term objectives.
Sometimes you have to sacrifice short-term gains to protect long-term success.
That's the price of thinking big.
Creating a Culture of Long-Term Thinking
If you want your team to think long-term, you've got to reward behaviours that support that.
Recognize and reward those who take calculated risks and make decisions that serve the long game.
Your culture should celebrate long-term wins over quick-fix gains.
Shifting to a Strategic Mindset
❸ No rigidity be agile.
Long-term success doesn't mean sticking to a rigid plan.
As the world changes -- so should your strategy.
Be prepared to adapt, change course, and adjust your strategy when needed.
It'll help you to keep your eyes on the future while staying flexible enough to navigate new challenges.
⚖ M-2.6.2 Short term results or long term results (II)?
Avoiding waste - Lean
❹ Short term improvements, window dressing by reports.
Producing more than what is needed is a waste. Lean production is lean especially because it produces only what is needed.
- Any type of transportation is waste. The less you transport, the better.
- Avoid unnecessary movements. Arrange everything so the worker has to move as little as necessary to assemble the product.
- Waiting: This refers primarily to people waiting. Not quite as important but also included are machines waiting.
- Over-processing refers to inclusion of additional features, parts, processes, or other things that the customer does not need and hence is not willing to pay for.
- Defects and Rework: Any product that does not satisfy the requirements and has to be reworked or thrown out.
- Inventory: Any kind of material you have but do not work on right now is a waste.
- Producing more than what is needed is a waste. Lean production is lean especially because it produces only what is needed..
Muda is well known but as even important are
mura muri .
They are:
Signals of a dysfunctional system that traditional management yields.
Managing waste - Lean
❺ Long term improvements, fix root casuses in the systems.
Go from fire-fighting everyday to using Lean Management towards world-class performance
(Jim Hudson 2024)
The seven wastes (along with low employee engagement) are the result of a dysfunctional system that traditional management yields ... EVERY SINGLE TIME without exception.
Fixing that is not about "chasing waste" out of the system it's about working on the system instead of working in it, where you're just fighting the fires (wastes) the dysfunctional system has created.
Lean, TPS & other forms of systems management are the ONLY way to systematically work on the system every day. EVERYTHING else (6 Sigma, Motivational Systems, Strategery, etc.) are futile unless the dysfunctional system is addressed first and foremost.
See the waste, find and eliminate the root causes, fix the systemic issues that enabled the faults and the waste in the first place.
Teach people how to see, how to think, how to take action, and how to behave to get the results they want instead of the results they are getting.
Then take those learnings, stabilize, standardize, improve.
⚖ M-2.6.3 A portfolio with specfications
Change in SAFE
❻ The scaled agile framework
SAFe did only focus on software deliveries in a top down micro-managed way.
A change in that in (2024) adding VSM and customer centric.
VSM safe
Please relax, fasten your seatbelts, and enjoy the wait. Everything is fine.
We will all be saved now. Value stream management will be used. And customer-centricity has a place.
See figure:
👉🏾 Still missing to get ready for the information age:
- Situation awarenees
- C&C change movement tot the edge
- A portfolio management system supporting all the information well structured.
From SAFe the portfolio:
Lean Portfolio Management Ready to start learning?
Use our finder to explore current offerings or learn more about a specific course Course.
See available classes. Learn more about the course LPM provides an alignment and governance model for a specific portfolio, which contains a set of Development Value Streams (DVS) for a business domain in an Enterprise.
Each DVS builds, supports, and maintains Solutions for Operational Value Streams (OVS).
🤔 These solutions are delivered by the OVS to the enterprise's external or internal Customers. ...
Modernizing portfolio management is critical to supporting the Lean-Agile way of working and competing in this new reality.
❼ When portfolio management is critical than why there are no products nor standards?
💡 The Jabes idea and proposal is covering that.
SIMF: the creation and optmizing cycle
❽ A building block for controlled improvements: understandable SIMF cycle.
Understanding the eight processes by the anatomy by their goals and activities:
- 1,2,3 geomappped roles by functions persons supporting the value stream
- 4,5,9 Profitable value streams by a well managed portfolio.
- 6,7,8 Technology for the product, service.
in a figure:
See right side.
The real value of this is only seen in the system as a whole.
Applicable for:
✅ Internal process improvements.
✅ product purpose usage improvements.
⚖ M-2.6.4 Purposeful products, services by an organisation
❾ Just some small adjustments from:
what is a business process
- A business product, service is a repeatable collection of steps a company uses to accomplish a goal.
- A product, service that you don't intend to repeat is an action plan instead of a true process. It's the difference between routine purchases and buying a new facility.
- A good product, service has built-in data-tracking steps, allowing you to compare performance and efficacy over time.
- A product, service should be adaptable to multiple situations so small changes to the work environment don't cause delays.
Furthermore, a good product, service should be easy to update in case of more significant or permanent adjustments.
That is a good understandable description for a business process, enterprise vision.
(There isn't more interesting information.)
Embedding the purposeful organisation
❿ Milestones: A product, service of an organsisation that lives in a social environment.
👉🏾 Milestone: An organisation understanding flow for their products, services.
Three essential criteria for products, services by an organisation:
- Repeatability: they must be designed to be repeatable.
- Transparency: need to be trackable, allowing you to monitor them for success.
- Agility: those that are set in stone don't hold up in the real world.
👉🏾 Milestone: An organisation having the persons with capabilities for their products, services.
For their products, services:
- Usefull: able to be used for a practical purpose or in several ways.
- Profitable: resulting in a net positive return, making it financially worthwhile.
- Explainable: reasons, causes, or mechanisms can be clearly described and justified.
M-3 Command & Control innovations and the future
M-3.1 Information processing in the information age
Information processing, administration using machines tools is a rather novelty for mankind.
Status:
- Became commodity for work flows in the 1990-s.
- Hypes based on tools technology, not the purpose.
- Focus internal organisational, not the customer.
Exceptions are successful organisation everyone wants to copy.
👉🏾
Preach: set the purpose, customer central.
✅ When the service for a customer is the core value dot it in a effective efficient way: no overburdening, no unnecessary complexity.
⚖ M-3.1.1 Effectivity, efficiency, lean, agility
Understanding lean
Seeing the conflict in lean, the root cause is by not having a well shared understanding in a definition of lean (why), what lean is about and how to use it.
Ask somebody what is:
- sales trade (process)
- a shaman (people)
- a ship (technology)
Anybody will come up with something that describes the shared understanding of what it is about.
Some will give a legal descriptions others what it is expected for usage, interacting.
Do this for lean and it will become unbearable in misunderstanding different opinions and worse.
More sensible is trying to solve that root cause.
My proposal: (correct it when it is wrong or incomplete)
- In the centre have a goal, there are also threats
- Three pillars, a/ people b/ technology /c process
- At each pillar simplicity is at the bottom, master of art at the top
- where to start?
At the bottom right side. For all levels of the goal something must be measurable at all levels (closed loops) when you want to see the effect of wanted improvements.
- How to proceed?
Go clockwise around in a cycle verify what is going on continuously.
- From right to left at the bottom (pull)
- Followed by left to right at the top (push)
In a figure:
see right side.
Misundertanding lean
The following is from B.Emilliani. pittyfull he don't want to help in understanding improving what is failing anymore.
Companies make a big mistake in implementing the Toyota production system thinking that it is just a production method.
The Toyota production method won't work unless it is used as an overall management system!
Those who decide to implement the Toyota production system must be fully committed.
If you try to adopt only the "good parts", you'll fail. (T. Ohno in NPS: New Production System, by I. Shinohara, Productivity Press, Cambridge, MA, 1988, p. 153 and 155)
Most organizations are led according to the strictures of classical management and processing is nearly always batch-and-queue.
So, your organization and situation is not nearly as unique as you think.
The facts is that organizations share many more similarities than differences, including:
- Every company does work
- All work is made up of processes
- All processes have customers and suppliers
- Just about every company does not understand the work
- All processing consists of value-added work and non-value-added but necessary work
- All processes contain waste, unevenness, and unreasonableness
- Every company has some combination of cost, delivery, quality, lead-time, and safety problems
- Process improvement works wherever material and/or information is processed and exchanged
- Process improvement applies to both repetitive and creative work
The shortcoming in this one is:
- Focus on internal activities claiming the same word customers for internal actions.
- Seeing only thy physical assembling line process.
- Missing the Customer centricity, delivering value by: a product / service for a purpose
- Missing the challenges of information processing, the information age
- At information processing there are new attention points:
- Information about persons, legal rights, health, situation, are a possible input resource
- The result for persons about persons, legal rights, health, are a possible resource by results that can act as input for other purposes, questions
- Doing research with descriptions on persons is sensitive by possible impacts but can help improving the social system.
⚖ M-3.1.2 Safety, Cyber security
Microsoft Safety, Cyber security 2024 trends
Microsoft Digital Defense Report 2024
Is not only about technical attention drawers but is making statements on what is to be done by the customers of the cloud, the technology offered as a service.
"Managing your own house"
Information processing is intangible wiht information security. (pag 56)
- Data doesn't move on its own. It'ss moved by people.
Because different people require different levels of access, a comprehensive data security policy must be dynamic, considering both data and user context.
This lets organizations balance protection and productivity, allowing low-risk users to continue working as usual while restricting the actions of users with elevated risk.
Securing organizational data has also become a multifaceted task, leading to the adoption of multiple, hard-to-manage tools.
This kind of fragmented approach creates more noise from duplicated alerts, making it harder to identify and investigate actual incidents.
...
- Accountability always starts at the top, with organizational leaders who not only understand their responsibility for security outcomes but ensure that security risk management is embedded across their business in an organization-wide and collaborative way
- Too often, IR teams find their customers don't have a reporting plan in place.
These aspects of accountability responsability at the customers of the cloud.
There are a lot of challenges to be solved to get this done well.
Optimizing governance and accountability
(pag 63)
Accountability always starts at the top, with organizational leaders who not only understand their responsibility for security outcomes but ensure that security risk management is embedded across their business in an organization-wide and collaborative way.
Leaders must establish a system of accountability, prioritization, and aligned incentives that is executed and monitored across the organization.
They must delegate risk accountability, mitigation implementation responsibility, and associated budgets/costs to leaders, managers, and individual contributors, as accountability alone cannot create a healthy culture.
Unfunded mandates or the belief that "security is the security team's job" will result in avoidable security weaknesses, increased burnout of security resources, and, in time, greater organizational cost.
Key elements sould include:
- Avoiding blame. Unless there is a clear violation of professionalism or failure of due diligence, avoid assigning blame for security incidents.
- Making sure learnings or issues don't slip through the cracks. Security issues are often discovered through critical thinking, fresh perspectives, and unexpected sources..
- Sharing responsibility. Organizational leaders must normalize security as part of everyone's job.
- Requiring cross-team training and learning. Fostering understanding, empathy, and repeatable cross-team processes enables teams to work well together on security.
Resilience maturity
(pag 66)
Within the dynamic realm of cybersecurity, the IR team regularly confronts a wide spectrum of customer challenges. Drawing from this rich experience, we have found that an organization’s resilience maturity can be determined based on four pillars: Operational, Tactical, Readiness, and Strategic.
- Operational For day-to-day IT operations, good preparation and maturity can ensure that an organization has good visibility of its estate, documented reliable playbooks, and rapid response capabilities based on automation.
- Tactical Prepare for initial response to an incident to respond logically and efficiently.
- Readiness Prepare for a cybersecurity incident.
- employees completed trainings and demonstrate understanding of material before granting access to company resources and data.
- Conduct continuous access reviews for company resources and data.
- Conduct tabletop exercises on a regular basis. Track and implement feedback and conclusions.
- Strategic Take steps to improve overall security posture in the longer term.
These are cultural and organisational aspects for the customers of the cloud.
There will be a lot of challenges to be solved to get this done well.
ACL Rbac Abac Pbac
Traditional solutions such as Access Control Lists (ACL) or Role-Based Access Control (RBAC) increasingly fall short in today's world.
These methods are too static for the complex, dynamic situations we face today.
Attribute Based Access Control (ABAC) offers a more modern approach.
Rules can be based on specific characteristics, such as: "only residents of the municipality of ....", and context, for example: "access only via corporate mobile, with two-factor authentication, and within the Kanaleneiland district". In addition, obligations can be added, such as keeping log files and deleting data after the retention period has expired.
But even that is not enough.
Rules are constantly changing, and the requirements around supervision are becoming stricter.
When rules are built into software, every change requires a new release.
Supervisors sometimes even have to view the source code during an audit.
This can and must be improved. The solution? Policy Based Access Control (PBAC).
We have investigated which languages, frameworks and providers are available and are curious about your experiences and insights.
Tools are made available but the customers of the cloud have to use them appropriate in achieving their safety goals.
Don't expect the technology being complete there are many gaps to be expected.
⚖ M-3.1.3 Knowing, managing, information customer related
problem solving the customer demand questions
efficient problem solving (igor-buinevici 2024)
Even though it may sound straightforward, Many people just forget about some steps, And then the process becomes inefficient.
There are 8 key steps of problem solving:
- Define the problem. Identify the problem, understand the context and implications.
"A problem well stated is a problem half solved." - John Dewey
- Gather Data. Accumulate relevant information through observation, research, and consultation.
Make sure you have all relevant resources for a comprehensive understanding of the issue and its underlying causes.
- Analyze Data Examine. the collected data systematically to identify patterns, trends, and relationships.
This will enable informed insights into the problem's nature and potential solutions.
- Generate Solutions/ Brainstorm a range of potential solutions, considering diverse perspectives and innovative approaches.
Try to generate the most effective solutions.
- Select Solution. Evaluate the generated solutions based on feasibility, impact, and alignment with objectives.
Selecting the most suitable course of action to implement.
- Plan Implementation. Develop a detailed plan outlining the steps, resources, and timeline required to execute the chosen solution effectively
Ensure clear communication and accountability.
- Implement & Test. Execute the planned solution, monitoring its implementation closely.
Gather feedback to assess its effectiveness and identify any necessary adjustments.
- Continue to Improve. Iterate and refine the implemented solution based on ongoing evaluation and feedback.
"Perfection is not attainable, but if we chase perfection we can catch excellence." - Vince Lombardi
Foster a culture of continuous improvement and innovation within the organization.
As you can see - one missing point can destroy the full process.
⚖ M-3.1.4 Knowing, managing, process results customer related
subjective-decision-making (igor-buinevici 2024)
Adjusting the topics in categories.
- Dimension People: Customers antipodes: Actors
- Dimension processes: Transformations, antipodes: Worldview
- Dimension machines: Owners dedcison makers, antipodes: Environmental constraints
(catwoe). In this to add is the:
- Dimension Purpose: Needs demands, problem. antipodes: Problem solvers, solutions
Objective analysis is always key in decision-making.
CATWOE analysis can help achieve a holistic understanding of the problem, systematic problem-solving, and engagement with all relevant stakeholders.
How to use this in practice:
- Define the problem and identify all 6 elements
- Analyze each point and overall insights
- Develop the most viable solutions
- Implement and monitor
M-3.2 Floor plans, optimizing value streams
Building any non trivial construction is going by several stages.
These are:
- high level design & planning
- detailed design & realisation
- evaluation & corrections
Non trivial means it will be repeated for improved positions.
👉🏾
Practice what your preach. ✅ When as a service provider the real lean culture is promoted for customers the service should be according the real lean service culture.
⚖ M-3.2.1 Aligning the Service organisation to the information age
Service as a Product, Information processing
Understanding SAAP,
how to Turn Professional Services Into Products
Product-based business models can help services firms achieve greater scale and profitability. But the transformation can be challenging.
Product management is one of the fastest-growing roles in business, having gained increased scope and importance in Silicon Valley.
While product managers used to be hired almost exclusively by technology companies, they are now being recruited in growing numbers by service-oriented businesses as well ...
Recognizing the challenges of margins and scalability, professional services firms are trying to evolve into product-like companies by productizing their services.
This involves automating, standardizing, and packaging aspects of a service into a tangible, repeatable, and scalable offering that is efficient to produce and easier to scale.
SAAP Strategic
Consideration to go for SAAP:
- Assess the product potential.
To what extent can the service be productized?
- Decide the optimal productization level.
To what extent should the service be productized?
- Define the offering portfolio.
What product-service mix should be offered to different customer segments?
- Build the product capabilities.
What are the enablers of productization, and how can these be leveraged to drive the productization process?
- Lead the transformation.
How should the productized organization be designed, and how can the barriers to change be overcome?
Turning services into products can be a lucrative pursuit, but it is fraught with operational and organizational challenges.
SAAP Tactic
Steps to achieve the SAAP state:
- Build a product culture and DNA.
Clearly articulate the vision and strategic importance of productization across the organization.
Embrace a product culture, including experimentation, risk-taking, innovation, and a focus on scalable solutions.?
- Establish a product management framework.
Create dedicated product management roles with clear responsibilities and objectives.
Invest in training existing staff members or hiring new talent with product management expertise.
Implement product management processes, such as design thinking and agile methodologies.
- Redesign compensation and career paths.
Develop compensation models that reward product development and management success. Create a parallel career path for product managers.
Include incentives that reward product success metrics like adoption rate, user satisfaction, and revenue generation.
- Adapt the go-to-market strategy.
Enable the sales team to sell productized services. Develop subscription- or consumption-based pricing models.
Communicate the value proposition of productized services to clients, focusing on the benefits of automation, consistency, and scalability.
- Balance standardization versus customization.
Offer a standardized core product with customizable add-ons or modules to cater to different customer segments or vertical markets.
If customers have heterogeneous preferences for human engagement, the services provider needs to have a portfolio of offerings featuring different levels of productization.
The dominant culture and mindset of professional services firms can be one major roadblock to transformation.
SAAP required changes
There is no free lunch in the required changes. A holostic service for a product is different than one for activities at demand.
Organizing a planned journey with special experiences is different than one that is only offering railway usage.
- Product organizations require very different KPIs, incentives, and career paths than service organizations, which are focused on billable hours, rates, and new-client acquisition
- An additional challenge is that these products are often "embedded" components of a service and are not sold as products, making it difficult to calculate revenue generated by the productized service.
- When services are productized, the standard time-and-materials business model used by professional services firms must be modified to allow for transaction- or outcome-based pricing.
Productized services should be priced on a per-task, per-document, or per-milestone basis.
⚖ M-3.2.2 Abstraction levels, closed loops in information context
Abstraction levels ordering
The axis in the six stages, ordered, organized.
At the third (vertical) a translation is made from wat is theory into a practical realization.
The conflict in Architecting how it should look like (theoretical) and engineering what is realistic possible (practical).
It more appropriate to see this as a dimension antipode moment. The world are too different than too see them being continuous.
Theoretical perspective top-down, bottom-up :
| theory | practical | SIMF | | Genba-3 | Genba-2 | Genba-1 | |
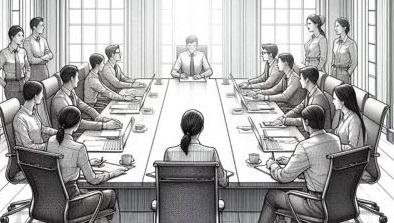 |
Context | Identify | Purpose | 1 0 ⬅ | Governance | Direction | Vision |
Content | Standardize | Plan | 2 9 ⬅ | Organisation | Form Texture | Requirements |
Logical | Harmonize | Engineer | 3 8 ⟳ | Information | Logical contents | Design |
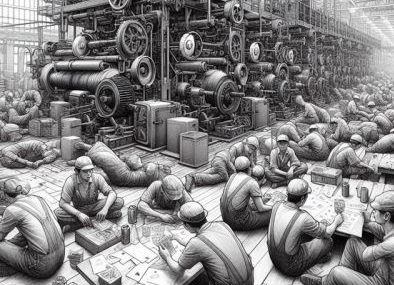 |
Operate | 3 8 ⟲ |
Physical | Incorporate | Skills | 4 7 ➡ | Data | Building blocks | Implement |
Details | Distinguish | Tools | 5 6 ➡ | ICT | Features | Evolve |
Practical perspective bottom-up, top-down:
| theory | practical | SIMF | | Genba-3 | Genba-2 | Genba-1 | |
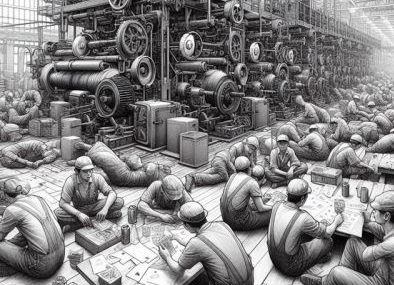 |
Details | Distinguish | Tools | 6 5 ➡ | ICT | Features | Evolve |
Physical | Incorporate | Skills | 7 4 ➡ | Data | Building blocks | Implement |
Logical | Harmonize | Operate | 8 3 ⟳ | Information | Logical contents | Design |
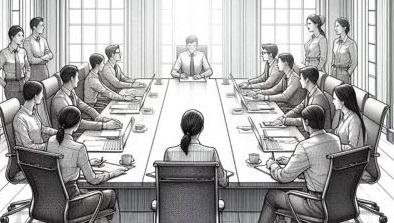 |
Engineer | 8 3 ⟲ |
Content | Standardize | Plan | 9 2 ⬅ | Organisation | Form Texture | Requirements |
Context | Identify | Purpose | 0 1 ⬅ | Governance | Direction | Vision |
Architecting engineering in Product service focus
The axis in the six stages, ordered, organized:
Abstract | | Words-1 | |
What | ➡ | Optimized business operations | 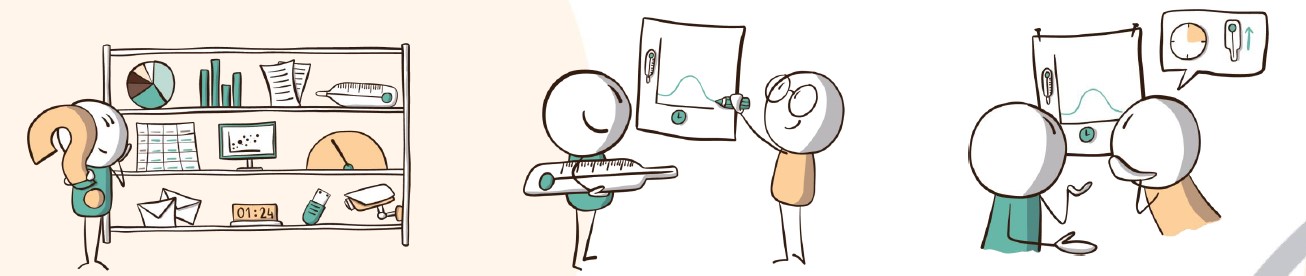 |
how | ➡ | Innovative service provision |
where | ➡ | Improved decision-making |
Who | ➡ | Control & Command | 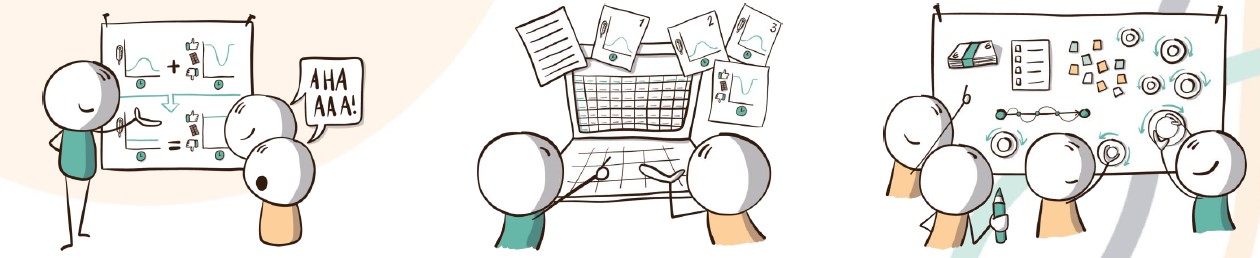 |
When | ➡ | Portfolio change & knowledge assurance |
Which | ➡ | Culture, Behaviour |
⚖ M-3.2.3 Understanding information, from data to insight
Data literacy
The goal is understanding learning capabilities how closed loops are used.
The axis in the six stages, ordered, organized:
Abstract | | Words-1 | |
What | ➡ | Recognize data for information | 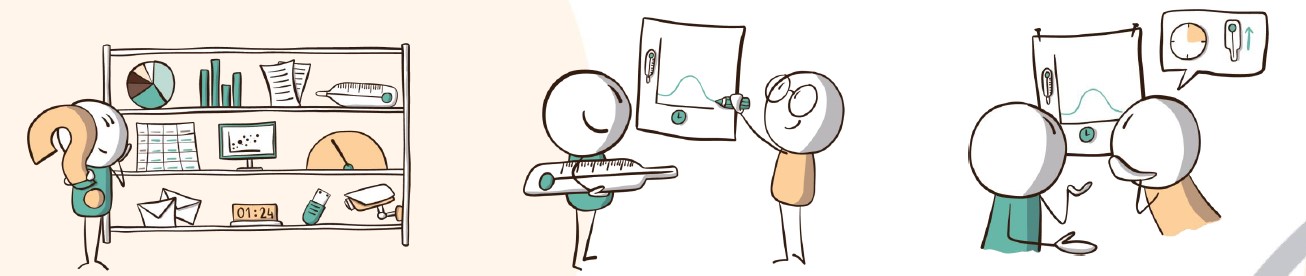 |
how | ➡ | Reading information |
where | ➡ | Understanding information |
Who | ➡ | Analysing - getting insight | 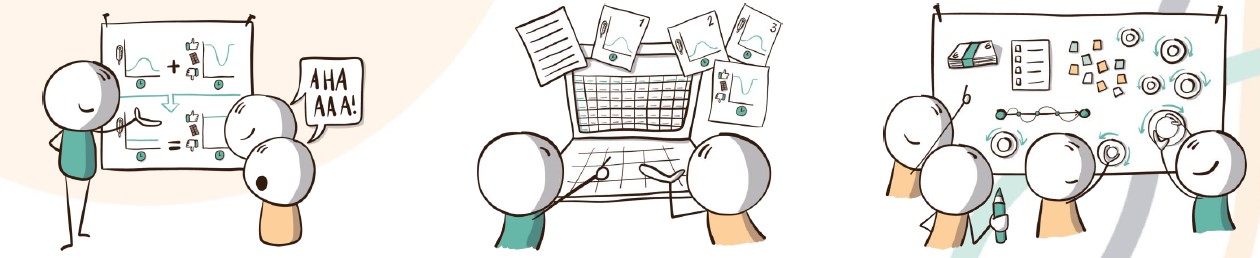 |
When | ➡ | Communicating insight |
Which | ➡ | Culture, Behaviour |
data, information life cycle
The goal is using the capabilities how closed loops are used to improve the SAAP.
The axis in the six stages, ordered, organized:
Abstract | | Words-1 | |
What | ➡ | Plan: Needed kind of information | 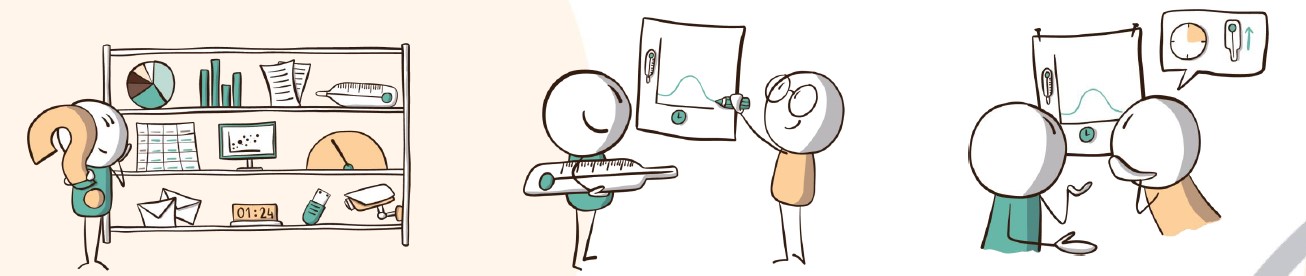 |
how | ➡ | Design: prepare, scales at measurements |
where | ➡ | Realisation: create data collectors |
Who | ➡ | Manage: store, archive or destroy | 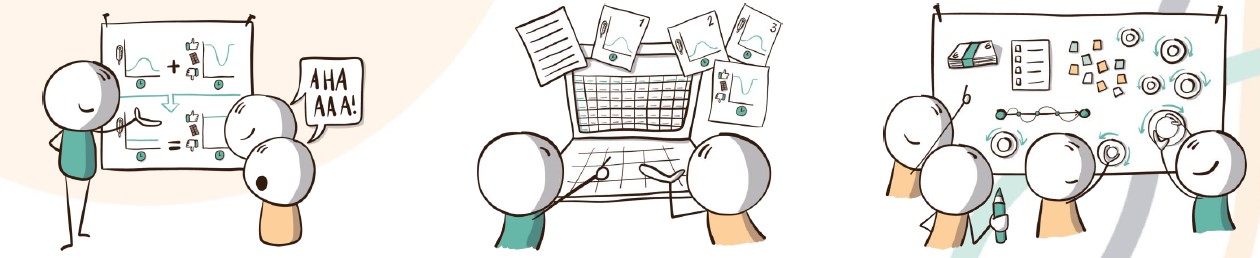 |
When | ➡ | Usage: simplistic specified measurements |
Which | ➡ | Insight: Getting wisdom, insights interactions of multiple measurements |
⚖ M-2.2.4 Aligning service provision in the information age
Customer focus data literacy
The axis in the six stages, ordered, organized:
Abstract | | Words-1 | |
What | ➡ | Customer Focus | 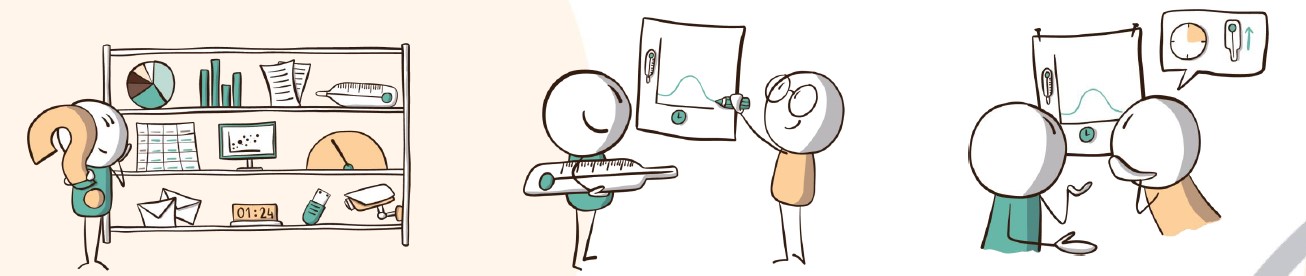 |
how | ➡ | Processes & Tools |
where | ➡ | Continous learning & improvements |
Who | ➡ | Teamstructure | 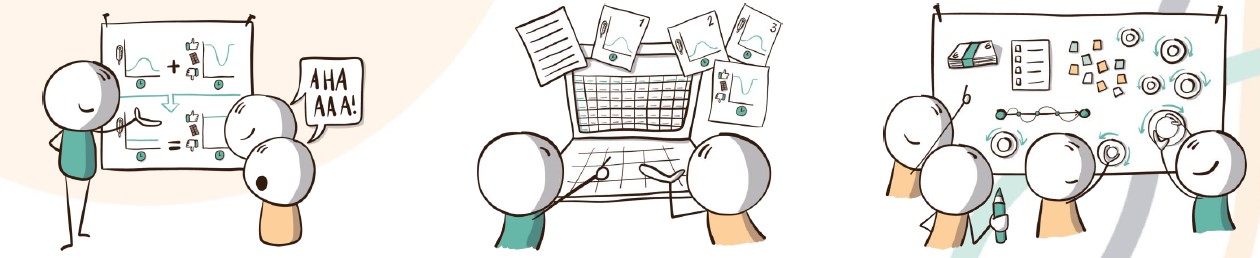 |
When | ➡ | Value stream management |
Which | ➡ | Culture |
The ist in service provision
Changes in the way of working are needed at a lot of levels. Top-down starts at 1.
👉🏾 The "ist" in a matrix (top-details, context-bottom):
| | |
| Customer | P&T | CLI | Teams | VSM | Culture |
| ➡ What | ➡ How | ➡ Where | ➡ Who | ➡ When | ➡ Which |
5 6 ➡ | Create software | Continuous rebuilding | waiting: instructions | Hierarchical orders | Continuation: bottlenecks | Following the leader |
4 7 ➡ | Software budgets | Prone to: manual defects | fixed skill set | Protecting knowledge | Keep status quo | No visions nor missions |
3 8 ⟳ | Talking: journey | Ad hoc - short term | ambiguous iterations | Following: hierarchy | No informed decisions | blaming culture |
3 8 ⟲ |
2 9 ⬅ | Technology delivery | Missing cooperation | mistakes = blaming | Responsibility: Line | No flow measurements | No trust nor openess |
1 0 ⬅ | Pushing technology | Lacking threat awareness | change aversion | Teams by identicalness | No flow optimisation | Ambiguity Obscurity |
The soll in service provision
Changes in the way of working are needed at a lot of levels. Bottom-up starts at 6
The differences are not in the dimensions but in the content of how it is implemented.
👉🏾 The "soll" in a matrix (top-details, context-bottom):
| | |
| Customer | P&T | CLI | Teams | VSM | Culture |
| ➡ What | ➡ How | ➡ Where | ➡ Who | ➡ When | ➡ Which |
6 5 ➡ | seek satisfaction | continuous improvement | quickly actions | organic autonomy | eliminate bottlenecks | diversity in thinking |
7 4 ➡ | visible deliveries | automate: no defects | evolving skills | knowledge sharing | balance: speed - quality | shared visions missions |
8 3 ⟳ | feedback loops | effective efficiency | small iterations | breaking hierarchy | informed decisions | safe, blame-free |
8 3 ⟲ |
9 2 ⬅ | value creation | collaboration | mistakes = learning | responsible autonomy | flow measurements | trust & openess |
0 1 ⬅ | Understand needs | lean: avoid 3m | adaption culture | diversity in teams | lean: flow optimisation | transparancy |
🎯💡 Promoting this way of working can be only succesfull by showing it by example.
M-3.3 Why to steer in the information landscape
Managing the goal for any non trivial construction follows several stages.
These are:
- high level strategy, vision & planning
- detailed strategy, missions & realisation
- evaluation & corrections
Non trivial means it will be repeated for improved positions.
Managing the process, information is needed for understanding what is going on.
Without knowing the situation or direction there is no hope in achieving a destination by improvements.
⚖ M-3.3.1 Customer centricity value streams
Change in SAFE
The scaled agile framework
SAFe did only focus on software deliveries in a top down micro-managed way.
A change in that in (2024) adding VSM and customer centric.
VSM safe
Please relax, fasten your seatbelts, and enjoy the wait. Everything is fine.
We will all be saved now. Value stream management will be used. And customer-centricity has a place.
See figure:
👉🏾 Still missing to get ready for the information age:
- Situation awarenees
- C&C change movement tot the edge
- A portfolio management system supporting all the information well structured.
From SAFe the portfolio solution-delivery:
The scaled agile framework
enterprise solution delivery
Large solution builders use specifications to manage requirements and designs, communicate them to system builders, and support compliance. The common specification process follows the ‘V’ model (left side of Figure 2), which typically results in large batches of upfront specification work that delay implementation and feedback.
While all the ‘V’ model activities (e.g., specifying requirements) are still critically important to solution development, in SAFe, engineers perform them concurrently and in smaller batches.
"Specify the system continuously and in smaller batches"
Is what the V-model was and is about in engineering for many years.
⚖ M-3.3.2 Failing management signals
Red flags
Bad management isn't always obvious at first. (Luke Tobin)
Here are 12 red flags to help you spot it.
Management isn't about having a title or power.
It's about setting an example.
12 warning signs that show poor management:
- Micromanagement: Constantly watching and controlling employees
- Poor Communication: Failing to share important information or unclear messages.
- Favouritism: Showing preferential treatment to certain employees.
- Blame Culture: Consistently focusing on finding fault.
- Lack of Accountability: Refusing to take responsibility for mistakes.
- Resistance to Feedback: Dismissing or reacting negatively to constructive criticism.
- Emotional Volatility: Displaying unpredictable mood swings.
- Short-term Focus: Prioritising immediate results at the expense of long-term growth.
- Neglecting Professional Development: Failing to invest in employee growth and skill advancement.
- Poor Work-Life Balance: Expecting constant availability and excessive working hours.
- Indecisiveness: Consistently struggling to make timely decisions.
- Lack of Vision: Failing to provide clear goals for the team or organisation.
Recognising these red flags is the first step towards solving them.
If you see any of these signs, it may be time to have a constructive conversation with management.
Don't settle for less than a healthy work environment.
In a figure:
See right side
⚖ M-3.3.3 learning - lean accounting
Static cost analyses
Lean Accounting: What's It All About? (2005 summit)
Bumping up against the accounting systems.
It soon becomes clear that traditional accounting systems are actively anti-lean:
- They are large, complex, wasteful processes requiring huge amounts of non-value work.
- They provide measurements and reports like labor efficiency and overhead absorption that motivate large batch production and high inventory levels.
- They have no good way to identify the financial impact of the lean improvements taking place throughout the company.
On the contrary, the financial reports will often show that bad things are happening when very good lean change is being made.
- Very few people in the company understand the reports that emanate from the accounting systems, and yet they are used to make important and far-reaching decisions.
- They use standard product costs which are misleading when making decisions related to quoting, profitability, sourcing, make/buy, product rationalization, and so forth.
Almost all companies implementing lean accounting are making poor decisions: turning down highly profitable work, out-sourcing products or components that should be made in house, manufacturing overseas products that can be competitively manufactured here at home, etc
Vision for Lean Accounting
We started with a vision statement and then drilled down to the practical tools used to make the vision a reality.
Our vision is that Lean Accounting will:
- Provide accurate, timely, and understandable information to motivate the lean transformation throughout the organization, and for decision-making leading to increased customer value, growth, profitability, and cash flow.
- Use lean tools to eliminate waste from the accounting processes while maintaining thorough financial control.
- Fully comply with generally accepted accounting principles (GAAP), external reporting regulations, and internal reporting requirements.
- Support the lean culture by motivating investment in people, providing information that is relevant and actionable, and empowering continuous improvement at every level of the organization
Conclusion
While Lean Accounting is still a work in-process, there is now an agreed body of knowledge that is becoming the standard approach to accounting, control, and measurement. ...
Companies using Lean Accounting have better information for decision-making, have simple and timely reports that are clearly understood by everyone in the company, they understand the true financial impact of lean changes, they focus the business around the value created for the customers, and Lean Accounting actively drives the lean transformation.
⚖ M-3.3.4 Three dimensions, Antipodes asteroide
Mathematical: Tetrahedron
M.C.Escher is most famous for the impossibilities in his art.
This one however is based on real mathematic figure.
Enclosed in a cube.
- eight corners, each connected to three others
- Four diagonals, not orthogonal, with antipodes
- six surfaces, a dice
- Three orthogonal dimensions, with antipodes.
Leaving one of the diagonals out for the changing purpose, flow, structure.
classic categories: people, process, machines
Using the three classic ones adding antipodes in a structure:
- people:
Working, producing, practical - administration, theoretical, manage
- process:
plan, coordinate supply, situation knowledge - plan, coordinate delivery, situation support
- Machines:
tools, working instructions, safety guidelines - purpose, usage guidelines, safety instructions
Three dimensions where the actions are trigerred by purpose.
The figure:
See right side
The teaser in this one are the interactions in the distortion.
Antipodes, different not connected worlds
The two sides at an axis have a differnt color (dark / light), they are different worlds in antipodes.
In the escher figure a clear segregation between the two is made isolating the threats by defensive walls.
Within the same color however it is possible to travel around.
This is philosofical a similarity:
- The line in the connection on the axis has a defensive wall. It is at:
- theoretical: 1 0 context, 2 9 content, 3 8 logical
- practical: 6 5 details, 7 4 physical, 8 3 logical
- Similar groups, within practical or within theoretical have bridges at the same level.
- The turning point, from practical to theoretical vice versa, on the axis is invisible.
M-3.4 Visions & missions in the boardroom
Managing the working force at any non trivial construction is moving power to the edges.
The cultural changes are:
- Accepting uncertainties and imperfections
- Trusting the working force while getting also well informed
- Respect for people, learning investments at staff
Non trivial means a complex or chaotic situation to get improved
Managing the working force at processes, information is needed for understanding what is going on.
Without knowing the situation or direction there is no hope in achieving a destination by improvements.
⚖ M-3.4.1 Structuring, engineering the enterprise
Inseparable product documentation layer
The operational performance of the organisation is having many dependencies.
"The core business" is the one that matters. The flow of that activity is a value stream.
Without understanding the structure of information processing no organisation can survive.
Enterprise engineering is trying to understand and optimise that.
Middleware the inverted pyramid
In 1968 a group of computer scientists gathered in Garmisch, Germany for what became known as the NATO Software Engineering Conference.
Conference attendee d’Agapeyeff presents this model as the stack that applications run on. He describes it as “very sensitive to weaknesses in the software”.
Refers to:
This sensitivity of software can be understood if we liken it to what I will call the inverted pyramid.
The buttresses are assemblers and compilers. They don’t help to maintain the thing, but if they fail you have a skew.
At the bottom are the control programs, then the various service routines. Further up we have what I call middleware.
This is because no matter how good the manufacturer’s software for items like file handling it is just not suitable; it’s either inefficient or inappropriate.
We usually have to rewrite the file handling processes, the initial message analysis and above all the real-time schedulers, because in this type of situation the application programs interact and the manufacturers, software tends to throw them off at the drop of a hat, which is somewhat embarrassing.
On the top you have a whole chain of application programs.
The point about this pyramid is that it is terribly sensitive to change in the underlying software such that the new version does not contain the old as a subset.
It becomes very expensive to maintain these systems and to extend them while keeping them live.
d'Adapeyeff - Software Engineering (1968) pg 14
Reusing this way layers and adding the stages when doing processing gives a foundation.
Demo inverted pyramid
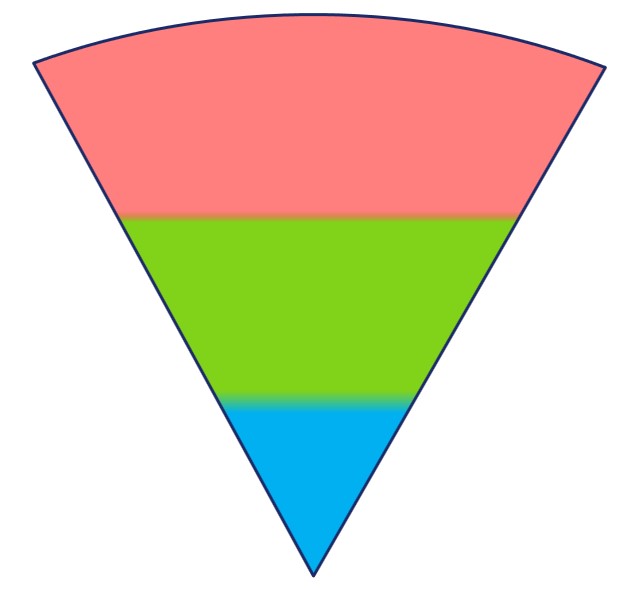
Separtions of concerns: shop-floor, administration, enterprise management:
- Core product (red)
- Administrative information, immediate by time belonging to the core product (green)
eg product properties, list of composing components
- Administrative information, different in time describing the product (green)
eg payment, product warrant, service moments
- Enterprise internal performance information, questions on what did it cost, the profits, customer satisfaction on the product and the service.
⚖ M-3.4.2 Enterpise structuring: cycles & multiple dimensions
Demo into four quadrants cycle
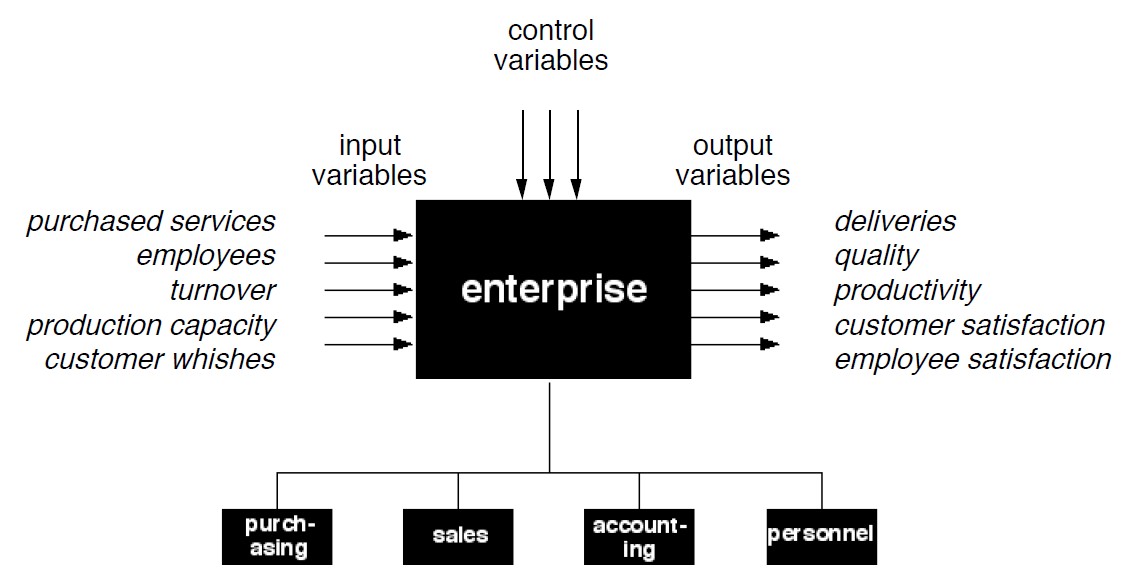
Although Demo is full on the ontology arround the product there is an image showing the flow:
- 🎭 input variables
- ⚙ Transforming by control variables
- 🎯ouput variables
- ⚖ Control: purchasing, sales, accounting etc.
That are for stages of situations these are the edges of four quadrants of a clockwise cycle.
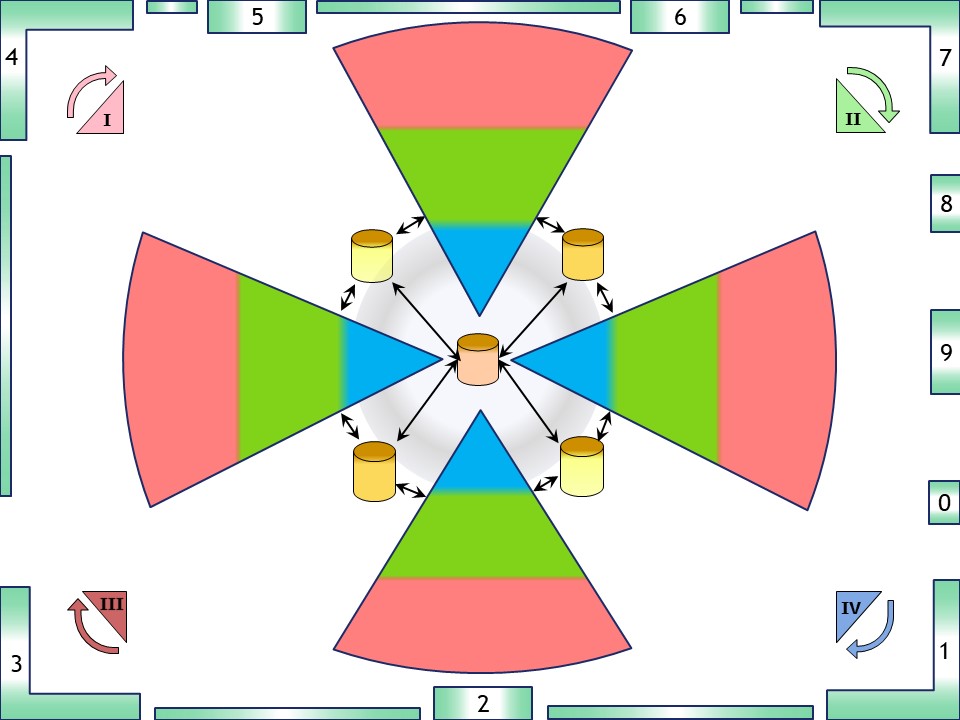
Those four quadrants edges are executed by siloed department lines, seperated by responsabilities.
The interactions with actions between departments are leading to complexity in the overall product flow.
details see link figure 👓
The success factor being mentioned in demo is solving a gap between department lines.
More specific the gap in the ordering (pull backend) and the delivery stage (push frontend) .
Adding Devils triangle & PDCA cycle.
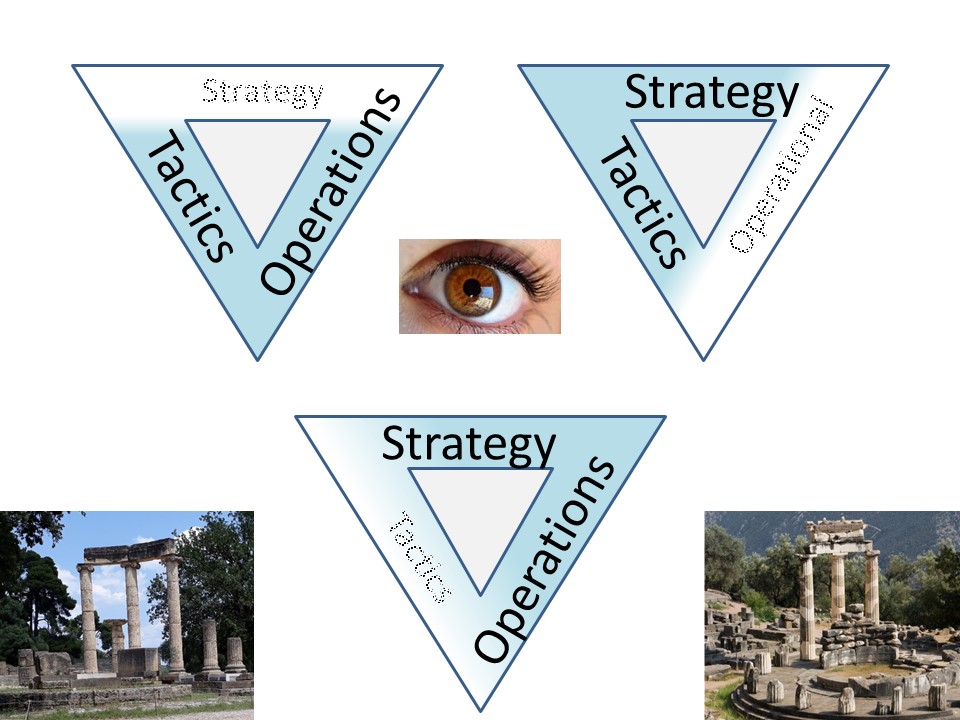
Having those three levels of: Strategy, Tactics, Operations, there is a need to find an optimal balance.
That optimal balance is almost impossible. As soon as two of the three are getting attracted the last one will get out of sight.
 
The one that is most likely to become the underdog an even get lost is the "operations".
That implies the core product, that what is mentioned as mission of an organisation will be lost.
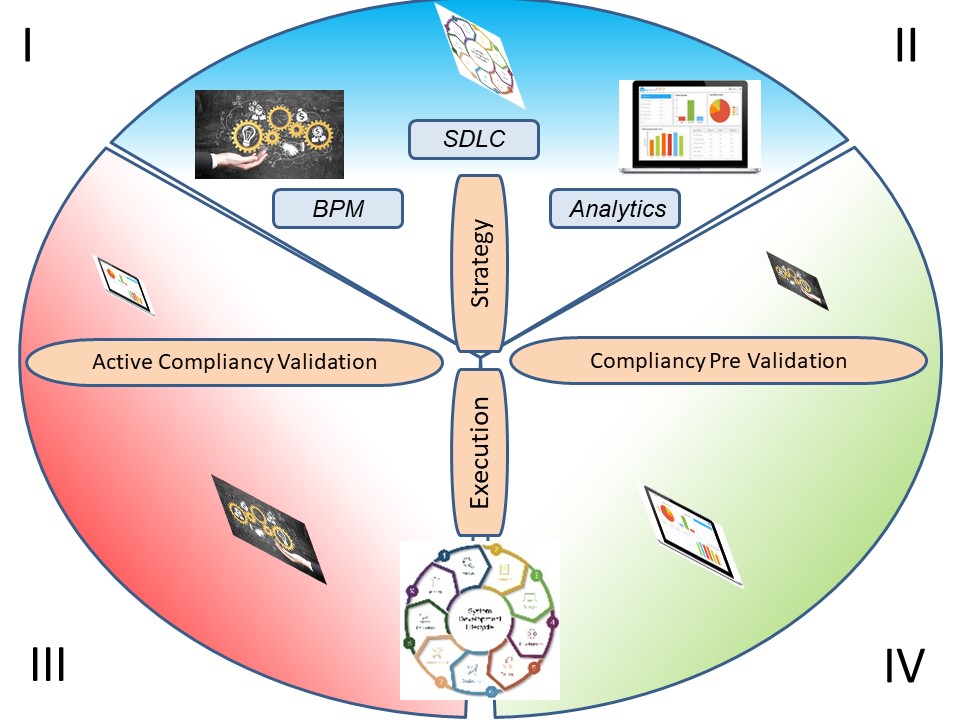
When putting Strategy & Tactics on top Operations at the bottom forming a triangle adding the process life cycle idea to that a process flow in quadrants and segments is building up.
details see link figure 👓
The operations is not at the same level as the two others. Additional representatives are needed at some places to fill the gaps for alignment of all three.
⚖ M-3.4.3 Optimising flows: removing constraints
Understanding the Theory of Constraints
Much More Than Production (2024 K.Kohls)
The Theory of Constraints (TOC) is a term that has sparked much debate and confusion. For many, the word "constraints" immediately brings to mind images of production lines and manufacturing bottlenecks.
This is where the confusion starts. Those unfamiliar with the breadth of TOC tools and techniques — including Drum-Buffer-Rope (DBR), Critical Chain Project Management (CCPM), Demand-Driven MRP (DDMRP), conflict resolution, reality trees, and much more — often reduce TOC to a mere production method.
In reality, TOC is a goal-based methodology with a vast scope of application that goes beyond the factory floor.
Laws vs. Theories: Clearing the Confusion
Before diving deeper, let's clarify the difference between a "law" and a "theory."
A law describes phenomena that have been observed consistently and predictably — think Newton's Law of Gravity, which explains how objects fall towards the Earth.
A theory, on the other hand, provides an explanatory framework for understanding how a complex system behaves — like Darwin's Theory of Evolution, which explains how species evolve over time.
And then there's Moore's Law, which, despite its name, isn't really a "law."
Moore's Law is an empirical observation about the doubling of computing power roughly every two years, but it lacks the consistency of a scientific law.
This distinction helps highlight why TOC is called a "theory."
It provides an explanation for why constraints exist and how they control a system, emphasizing the critical role of a single limiting factor.
Constraints: More Than Just Production Bottlenecks
The concept of a constraint in TOC is broad. A constraint can be anything that limits progress towards achieving a goal — a policy, a metric, a conflict, or a physical bottleneck. In a production system, the most common type of constraint is often called a bottleneck: a point where demand exceeds capacity, limiting the rate of output.
But it's important to understand that not all constraints are production bottlenecks.
A common non-production constraint is the conflict between focusing on increasing the flow of money into an organization — what TOC calls "Throughput" — and using conventional profit calculation methods. Throughput, in TOC, refers to the rate at which an organization generates money through sales, rather than simply using profit as a static number derived from subtracting costs.
From a personal perspective, throughput can be thought of as the rate at which one progresses towards a goal.
This definition can be confusing, as many in production think of throughput purely as a rate of output, not as a financial measure.
The Role of Bottlenecks and Constraints in TOC
The bottleneck controls throughput, but the goal of the system dictates what that bottleneck is.
For example, if the goal is to increase the flow of parts through production, then the constraint is the bottleneck limiting that flow.
However, if the goal is to maximize profitability, the bottleneck might be something entirely different, such as market demand or a restrictive policy.
There is inherent simplicity in this logic, yet many critics of TOC fail to understand the difference between a bottleneck, which deals with the flow of objects (e.g., parts, claims), and a constraint, which limits progress towards a broader goal.
In TOC, a bottleneck is a specific type of constraint that relates to the flow of tangible items or tasks through a system. For example, just as parts move through a manufacturing line, insurance claims move through an administrative system. Both can experience bottlenecks.
However, a constraint in TOC is more than just a bottleneck; it represents anything that holds back the system from achieving its goal.
System Optimization vs. Local Optimization
The goal of TOC is always system optimization, not local optimization. System metrics, such as overall throughput, cycle time, and variability, must be optimized for the entire production system.
In contrast, trying to improve efficiency at each individual station is called local optimization, which often leads to suboptimal results for the broader system.
A reduction in cost at one station, for instance, may not translate to increased profitability for the entire operation if it does not address the system's constraint.
This is why TOC focuses on the constraint, not on cost reduction at every point in the process.
It is difficult to demonstrate profit gains from reducing costs in isolation, but by increasing throughput -the flow of money- the impact on system performance is clear and measurable.
Why "Constraints" and Not "Constraint"?
The name "Theory of Constraints" is plural for a reason. As a system evolves, its constraints change.
Continuous improvement inevitably shifts bottlenecks from one part of the process to another.
Today's constraint might be a lack of production capacity; tomorrow's could be market demand.
TOC acknowledges that constraints are dynamic, and continuous improvement must adapt as the entity's goals change.
⚖ M-3.4.4 Optimising flows: budget, design, production
budgetting & performance
Searching unlimited growth (2024 Rajdeep Ghai)
Budgeting and performance management destroy more companies, initiatives, and careers than we can ever know.
Corporate processes are the bane of excellence.
And the key to unlocking organization wide excellence is in corporate processes.
To solve is an approach to:
- Visualize the 12 most important and critical corporate processes
- Quantify their impact on the customer and the business
- Simplify, and transform corporate processes, and
- Manage them efficiently and effectively in order to drive corporate growth and success.
The reason why your transformations fail, agile gives superficial benefit, and you are nowhere near excellence, is that you are solving the wrong problem in the wrong place
Design & production
Tech software-engineering
review of the 1968 NATO Software Engineering Conference.
Reference to:
Software production takes us from the result of the design to the program to be executed in the computer.
The distinction between design and production is essentially a practical one, imposed by the need for a division of the labor.
In fact, there is no essential difference between design and production, since even the production will include decisions which will influence the performance of the software system, and thus properly belong in the design phase.
For the distinction to be useful, the design work is charged with the specific responsibility that it is pursued to a level of detail where the decisions remaining to be made during production are known to be insignificant to the performance of the system.
Naur - Software Engineering (1968) pg 20
Design is continuously evolving, and during implementation the writers of software discover new things and need to make decisions on the fly.
Reference to:
Honestly, I cannot see how these activities [Design, Production] allow a rigid separation if we are going to do a decent job.
If you have your production group, it must produce something, but the thing to be produced has to be correct, has to be good.
However, I am convinced that the quality of the product can never be established afterwards.
Whether the correctness of a piece of software can be guaranteed or not depends greatly on the structure of the thing made.
This means that the ability to convince users, or yourself, that the product is good, is closely intertwined with the design process itself.
Dijkstra - Software Engineering (1968) pg 20
"An unsolved problem in Software Engineering today is how we can resolve and align internal and external designs and documentation.
Complex systems typically have hundreds of pages of customer documentation describing how the system works and what actions they need to take to get the outcome they want."
M-3.5 Sound underpinned theory, improvements
Knowing the position situation in by observing several types of associated information .
These are:
- Kind of task in the process by role
- Art of the role by observed input and results
- Art of the role by follow up interactions
Non trivial means it will be repeated for improved positions.
Command & control needs information for what understanding what is going on.
Without knowing the situation or direction there is no hope in achieving a destination by improvements.
⚖ M-3.5.1 A structured enterprise, organisation
Mastering the purpose knowing the tools
Given tools working bottom-up to the purpose.
Both tools and purpose are left out in the generic approach, four of the six levels are left.
- skills aligned functionality & safety for who is doing what activities in "best practices"
- Preparations of product, service in the operational cycle
- Preparations for product, service change in the engineering cycle
- skills aligned for stability, finance, mandatory legal obligations
in a figure:
Mastering to get tools knowing the purpose
Given a purposes working top-down to tools.
Both tools and purpose are left out in the generic approach, four of the six levels are left.
- skills aligned for change, innovation, marketing, future revenue
- Support for product, service creation & changes in the engineering cycle
- Support of product, service deliveries in the operational cycle
- skills aligned for functionality & safety for who is doing how activities by "best practices"
in a figure:
⚖ M-3.5.2 Change process in a structured enterprise, organisation
SIMF understanding the management improvement cycle
- A vision: Product / Service
- Geo-mapped roles
- Persons methodologies
- Flows, value streams
- Optimizing at constraints
- Functionality, technology
- Safety, technology
- Product Service knowledge
in a figure:
See right side.
SIMF applying with processes and deliveries in an improvement cycle
These are:
- Improving the organisation: the interactions processes by command &control and technology
This is at centre inside vertical plane of the cubicle, from administrative activities to processing by workers.
- Improving the product, service: the flows by functional backend to functional frontend.
This is at centre inside vertical plane of the cubicle, from back-end to front-end.
⚖ M-3.5.3 Changing the structured enterprise, organisation
Improving the organisation
Given a purposes working top-down to tools.
Both tools and purpose are left out in the generic approach, four of the six levels are left.
- skills aligned for change, innovation, marketing, future revenue
- Support for product, service creation & changes in the engineering cycle
- Support of product, service deliveries in the operational cycle
- skills aligned for functionality & safety for who is doing how activities by "best practices"
in a figure:
Improving the product, service
in a figure:
⚖ M-3.5.4 Three dimensional anatomy maps, PDCA cycles
Applying the Simf cycle
This is possible for:
- Improving the product, service.
- Improving the organisation: production, perorations, process, and results.
closed loops limitations in antipodes
There are three closed loops at each Simf cycle:
- The theoretical closed loop: upper two levels.
- The practical closed loop: bottom two levels
- The holostic closed loop clossing the bottom and top levels.
🎯💡 Promoting this way of working can be only succesfull by showing it by example.
M-3.6 Maturity 5: Strategy visions adding value
From the three PPT, People, Process, Technology interrelated areas in scopes.
- ✅ P - processes & information
- ✅ P - People Organization optimization
- ✅ T - Tools, Infrastructure
Only having the focus on others by Command and Control is not complete understanding of all layers, not what Command & Control should be.
Each layer has his own dedicated characteristics.
⚖ M-3.6.1 The product, service positioned within a system
Systems thinking, the properties of the whole
❶ Systems the interactions of parts.
systems thinking
Machines, organizations, and communities include and are themselves part of systems.
Russell L. Ackoff a pioneer in systems thinking defined a system not as a sum of its parts but as the product of its interactions of those parts.
".. the essential properties that define any system are the properties of the whole which none of the parts have."
The example he gives is that of a car.
- The essential property of car is to take us from one place to another.
- This is something that only a car as a whole can do.
- The engine by itself cannot do this.
- Neither can the wheels, the seats, the frame, and so on.
❷ systems thinking (video),
Ackoff continues:
"In systems thinking, increases in understanding are believed to be obtainable by expanding the systems to be understood, not by reducing them to their elements.
Understanding proceeds from the whole to its parts, not from the parts to the whole as knowledge does."
A system is a whole which is defined by its function in a larger system of which it's a part.
For a system to perform its function it has essential parts:
- Essential parts are necessary for the system to perform its function but not sufficient
- Implies that an essential property of a system is that it can not be divided into independent parts.
- Its properties derive out of the interaction of its parts and not the actions of its parts taken separately.
When you apply analysis (reductionism) to a system you take it apart and it loses all its essential properties, and so do the parts.
This gives you knowledge (know how) on how the part works but not what they are for.
To understand what parts are for you need synthesis (holism) which considers the role the part has with the whole.
Why is this important and what has this to do with quality, safety, environmental and regulatory objectives?
Systems thinking, not each of the parts
❸
The answer is that when it comes to management systems we often take a reductionist approach to implementation.
We divide systems into constituent parts and focus our implementation and improvement at the component level.
This according to Ackoff is necessary, but not sufficient for the system to perform.
- We only need to look at current discussions with respect to compliance to understand that the problem with performance is not only the performance of the parts themselves, but rather failures in the links (i.e. dependencies) the parts have with each other.
- Todd Conklin (Senior Advisor to the Associate Director, at Los Alamos National Laboratory) calls this "between and among" the nodes.
To solve these problems you cannot optimize the system by optimizing the parts making each one better.
You must consider the system as a whole – you must consider dependencies.
- However, this is not how most compliance systems are implemented and improved.
Instead, the parts of systems are implemented in silos that seldom or ever communicate with each other.
Coordination and governance is also often lacking to properly establish purpose, goals, and objectives for the system.
In practice, optimization mostly happens at the nodes and not the dependencies.
It is this lack of systems attention that contributes to poor performance.
No wonder we often hear of companies who have implemented all the "parts" of a particular management system and yet fail to receive any of the benefits from doing so.
For them it has only been a cost without any return.
However, by applying Systems Thinking you can achieve a better outcome.
"One can survive without understanding, but not thrive. Without understanding one cannot control causes; only treat effect, suppress symptoms.
With understanding one can design and create the future ... people in an age of accelerating change, increasing uncertainty, and growing complexity often respond by acquiring more information and knowledge, but not understanding." (R.Ackoff)
⚖ M-3.6.2 Compliancy at an organisation, products, services
Practice what you preach
❹ This structured approach for C&C has implications on how to organize C&C.
- The service organisation, practical realisations, is expected to have a pro-active collaborative way of working.
- The C&C high perspective although positioned in the theoretical administrative plane is expected to coordinate all planes over all levels.
It is the centre in all floorplans.
- Coordination over all planes over all levels is breaking the siloed hierarchical and siloed dimensions assumption.
Four levels, three cycles
traditional versus operational approach to compliance (Raimund Laqua)
To contend with compliance, operational, and technical uncertainty, organizations often adopt management systems standards such as ISO 37301 (Corporate Compliance), ISO 14001 (Environment), ISO 31000 (Risk), ISO 9001 (Quality), ISO 55000 (Assets), and so on.
The concept of operations (CONOPS) for these management system standards varies but each follows a similar model.
in a figure:
See right side.
❺ There is no simple solutions by implementing the parts.
Compliance is more than the sum of its parts
None of the parts of a compliance system individually can effectively contend with risk.
Instead, they all must work as-a-whole to provide effective layers of defence against the effects of uncertainty to avoid or minimize the number of incidents, injuries, loss time, claims, emissions, spills, violations, and so on.
Partial implementation results in sub-optimal performance that will weaken the ability of a compliance system to be effective.
Systems without programs will sub-optimize for efficiency. Programs without systems seldom achieve consistent performance.
Processes without systems suffer from lack of consistency and conformance to standards and regulations.
Processing by attributes
Nice three dimensions: information, experience, emotion
- information - emotion = fact
- information + experience = opinion
- - information + experience = ignorance
- - ( information - experience ) = stupidity (ingnores fact)
there must be more combinations.
15 rules every ceo should-know
❻ No 16: Everyone is a CEO as part in the whole of the whole system.
"The main thing is to keep the main thing the main thing." (Stephen Covey)
⚖ M-3.6.3 Optimizing an organisation, products, services
Theory of constraints, solving bottlenecks
❼ When there is a piling up in requirements and deliveries are blocked there is a constraint.
Solve the constraint!
Focccus:
tocpa expert (clarke-ching 2018)
- Find (Bottleneck)
- Optimise (Bottleneck)
- Coordinate (Non Bottleneck)
- Collaborate (Non Bottleneck)
- Curate (Non Bottleneck)
- Upgrade (Bottleneck)
- Start Again, Strategically
Non Bottlenecks refer indirectly to bottlenecks.
SIMF: the creation and optmizing cycle
❽ As a building block for controlled improvements the SIMF cycle is understandable.
The real value of this is only seen in the system as a whole.
Understanding the eight deliveries by the anatomy by their goals and activities:
- 1,2,3 geomappped roles by functions persons supporting the value stream
- 4,-,9 Profitable value streams by a well managed portfolio.
- 6,7,8 Technology for the product, service.
in a figure:
See right side.
The real value of this is only seen in the system as a whole.
Applicable for:
✅ Internal process improvements.
✅ product purpose usage improvements.
When portfolio management is critical than why there are no products nor standards for it?
💡 The Jabes idea and proposal is covering that including change.
⚖ M-3.6.4 The purposeful organisation, products, services
Building the purposeful organisation
❾ Just some small adjustments from:
what is a business process
- A business product, service is a repeatable collection of steps a company uses to accomplish a goal.
- A product, service that you don't intend to repeat is an action plan instead of a true process. It's the difference between routine purchases and buying a new facility.
- A good product, service has built-in data-tracking steps, allowing you to compare performance and efficacy over time.
- A product, service should be adaptable to multiple situations so small changes to the work environment don't cause delays.
Furthermore, a good product, service should be easy to update in case of more significant or permanent adjustments.
Embedding the purposeful organisation
❿ Milestones: A product, service of an organsisation lives in a social environment.
👉🏾 Milestone: Success of an organisation for their products, services defined targets.
Three essential criteria for products, services by an organisation:
- Repeatability: they must be designed to be repeatable.
- Transparency: need to be trackable, allowing you to monitor them for success.
- Agility: those that are set in stone don't hold up in the real world.
👉🏾 Milestone: Success of an organisation within the social environment .
For their products, services:
- Purposeful: They should serve a purpose for the social community.
- Environment: There should be no unacceptable negative impact on the natural environment.
- Egalitarian: All being involved should benefit and be treated in a explainable same way.
⚖ M-3.6.5 Following steps
These are design data concepts, others:
Meta, describing data 👓 next
bianl previous, business Intelligence & Analytics.
Others are operational realisations: 👓
data meta math
© 2012,2020,2024 J.A.Karman